- цемента, в качестве основного вяжущего;
- химических добавок;
- органических заполнителей (измельченные деревянные отходы, дробленые стебли льна, хлопчатника, камыша, конопли, рисовая солома, лузга подсолнечника и др.).
После смешивания компонентов (в определенной пропорции) добавляется вода. Полученная арболитовая смесь формуется и подвергается вибрационному воздействию для получения плит или блоков. Поскольку в качестве наполнителя используется сырье органического происхождения, арболит имеет второе название – деревобетон.
Отечественный органический бетон является аналогом голландского, который производится по оригинальной технологии Durisol.
Основными наполнителями органического бетона, производимого в нашей стране, являются деревянная щепа и древесные опилки. Готовый блок имеет рельефную структуру, с хорошо просматриваемой фактурой наполнителя. Структура бетона может быть плотной, пористой или крупнопористой. Более высокие эксплуатационные характеристики свойственны материалу, в котором содержится больше щепы, чем опилок.
Области применения и форма выпуска
Легкий бетон на органических заполнителях и строительные материалы, изготовленные из него, используют для строительства частных малоэтажных домов и других построек, несущие стены которых не подвергаются большим нагрузкам на сжатие. Согласно ГОСТ Р 54854-2011, арболит применяют в следующих областях:
- в качестве монолитной теплоизоляции и звукоизоляции кровель, чердаков, перекрытий, трехслойных панелей, плит перекрытий и покрытий, полов;
- для возведения несущих, внешних стен и внутренних перегородок;
- для сборно-монолитных стен;
- как элементы несъемной опалубки.
Марка бетона зависит от испытываемых в конструкциях нагрузок. Наружная и внутренняя стороны блока должны иметь отделочный слой.
Это обеспечит их защиту от излишнего увлажнения и последующего разрушения.
Есть несколько разновидностей арболита. К ним относятся:
- Применяют для возведения стен малоэтажных домов, хозяйственных построек и промышленных объектов. Самый распространенный размер блока составляет 500×300×200 мм.
- Плиты покрытия для кровель и стен.
Используются в качестве теплоизоляционного и звукоизоляционного внешнего покрытия.
- Жидкая смесь
или Применяется для заливки опалубки при возведении монолитных частей конструкции.
Арболитовый блок
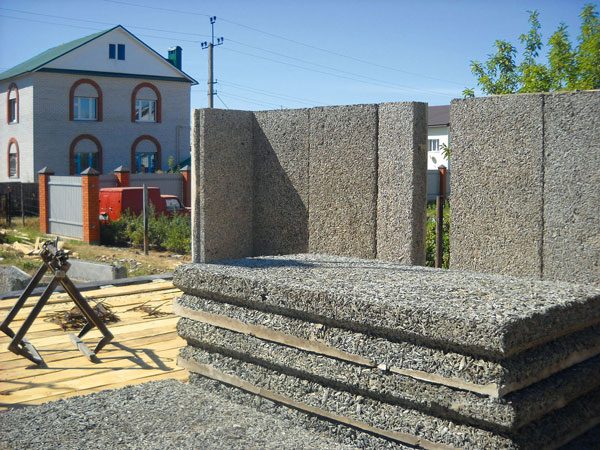
Производство органического бетона выполняется в соответствии с требованиями СП 63.13330.2012 и СН 549-82. Размер строительных блоков не имеет установленных стандартных размеров. Он регулируется внутренними нормами предприятия и может отличаться у разных производителей.
Химический состав
Технология производства и состав арболитовой смеси зависит от предприятия-изготовителя. Состав легкого органического бетона регламентируется ГОСТ 27006-86 (Правила подбора состава бетонов) и внутренней технической документацией предприятия.
Для его производства используют несколько составляющих.
Минеральные вяжущие
В качестве основного компонента, связывающего органический заполнитель, в легком бетоне выступает портландцемент. Согласно требованиям ГОСТ 10178-85 и ГОСТ 31108-2003, марка используемого цемента должна быть не ниже М400. Если производство арболитовой смеси приходится на зимний период, рекомендуется использовать портландцемент марки ПЦ 500Д0. Допустимо применение малоклинкерных цементов с минеральными добавками (МКВ), вяжущих низкой водопотребности (ВНВ) и тонкомолотых цементов (ТМЦ).
Заполнители
Основным заполнителем для деревобетона является измельченные древесные отходы, полученные при переработке деревьев хвойных и лиственных пород. В качестве наполнителя применяется как один тип органического материала, так и комплексное совмещение разных наименований и фракций растительного сырья. Более качественный бетон получается при использовании деревянной щепы.
Древесные заполнители должны соответствовать следующим требованиям:
- максимальный размер частиц калибруется в пределах 5 мм по толщине, 30 мм по длине и 10 мм по ширине;
- содержание полисахаридов в сырье не должно превышать 2%;
- допустимый процент примеси листьев и хвои (в сухой массе) должен находиться в пределах 5% и 10%, соответственно.
Органическое сырье не должно содержать плесени, гниющих частиц и инородных вкраплений
(земля, металлические частицы, глина, лед и пр.). Если наполнителем выступает стружка, опилки или их смесь, размер сырья не нормируется.
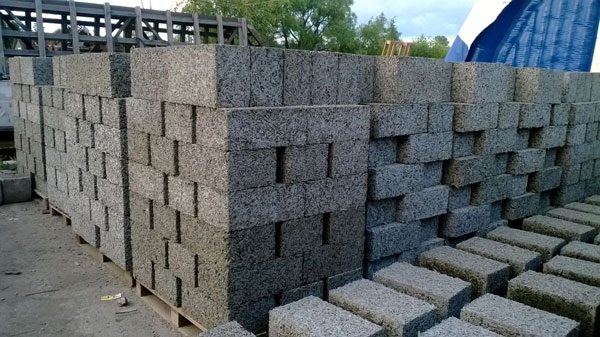
Химические добавки
Поскольку в состав арболита входят органические заполнители, требуется добавление химических компонентов. Химикаты позволяют сохранить целостность биологического сырья и ускоряют адгезию с цементом, сокращая время твердения бетона.
Они также регулируют пористость конечного продукта и способствуют предотвращению коррозии взаимодействующих стальных элементов. Для производства органической бетонной смеси требуются следующие вещества:
- сульфат алюминия;
- нитрат кальция;
- хлорид кальция;
- хлорид аммония;
- сернокислый глинозем;
- жидкое стекло.
Критерии эффективности химических добавок регламентируются ГОСТ 24211-2008. Добавки смешиваются с водой, затем добавляются к цементно-древесной смеси. Эти добавки совершенно не опасны для здоровья.
Вода
Качество воды, используемой для производства деревобетона, указано в ГОСТ 23732-79. Она должна быть пресной, без содержания жиров и их производных, а также красящих примесей. Требуемое содержание ПАВ, фенолов и полисахаридов – не более 10 мг/л, ионов хлора – не более 300 мг/л.
Вода и раствор химикатов проходят лабораторный контроль.
Его проводят для каждого нового источника поступления воды или для каждой партии приготовленного химического раствора. Качество воды может оцениваться по данным санитарной организации, контролирующей ее качество.
Основные технические характеристики этого материала
Арболит должен соответствовать следующим качественным показателям:
- Средняя плотность
(кг/м 3). Для теплоизоляционного материала установлены марки D300-D500. Марки конструкционного арболита – от D500 до D900.
- Прочность на сжатие.
Бетон соответствует разным классам прочности (В0,35, 0,75 – для одноэтажных зданий и В1,5, 2,5, 3,5 – для двухэтажных). Арболит имеет марки М2,5, М3,5, М5, М10. В зависимости от этого показателя определяется вид и функциональное назначение материала.
- Теплопроводность.
Этот показатель позволяет определить необходимую толщину стен. Поскольку арболитовый материал имеет низкий коэффициент теплопроводности, это позволяет использовать его при строительстве в зонах с холодным климатом. В ГОСТ Р 54854-2011 установлены коэффициенты теплопроводности (Вт/(м·К)), в зависимости от марки бетона (D300 – 0,07, D500 – 0,95, D800 – 0,17).
- Влагопоглощение и паропроницаемость.
Эти показатели регламентируются нормами ГОСТ 4.212-80. Коэффициент водопоглощения для арболита составляет 75 – 85%, паропроницаемость – до 35%.
- Морозостойкость
. Этот коэффициент показывает устойчивость материала к воздействию переменных циклов заморозки и оттаивания. Для конструкционно-теплоизоляционного деревобетона установлены марки по морозостойкости F15, F25, F35, F50.
- Усадка.
Испытания показывают, что легкий органический бетон подвержен минимальной усадке, которая находится в пределах 0,8%.
- Огнестойкость.
К этому показателю предъявляют несколько требований пожарной безопасности. Марки от D400 должны соответствовать группе горючести Г1, токсичности продуктов горения Т1, воспламеняемости В1 (ГОСТ 30244, 12.1.044, 30402). В соответствии с этими показателями, арболит является трудногорючим материалом, с малым количеством выделяемого дыма.
- Звукоизоляция.
Теплоизоляционные арболитовые материалы имеют высокие звукоизоляционные свойства, с коэффициентом шумопоглощения до 0,6 ДБ.
Свойства разных видов деревобетона зависят от используемой марки цемента, химических добавок, технологии производства и материала, защищающего наружные части арболитовых блоков.
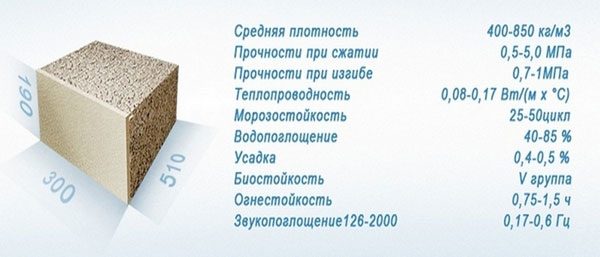
Испытания для контроля качества
Прежде, чем выпустить арболит в продажу, предприятие изготовитель проводит серию испытаний
. Контроль качества включает следующие испытания:
- определение гранулометрического состава заполнителя;
- оценка всех качественных показателей материала по ГОСТ 10181 (теплопроводность, прочность, паропроницаемость, пожаробезопасность и др.);
- проверка радиационных показателей и соответствие санитарно-гигиеническим требованиям.
По результатам проверки материал получает сертификаты соответствия и отправляется на реализацию. Сертификаты подтверждают безопасность арболита для здоровья человека.
Виды легкого органического бетона
В классификации по назначению выделяют два вида арболита. Один предназначен для внутренних работ, другой можно применять как для возведения несущих стен, так и для утепления конструкции здания.
Теплоизоляционный тип
Выпускается в виде блоков и плит, плотностью не более 400 кг/м 3 . Предназначен для возведения внутренних перегородок или утепления стен, полов и кровель. Плиты производят с добавлением пенообразователя и водоразбавляемой смолы, что повышает прочность на изгиб, с сохранением исходной плотности материала.
Термоизоляционные плиты представлены следующими вариантами:
- стеновые панели (28×118×229);
- панели узкие (28×58×229);
- панели оконные (30/40×60×230).
Такие материалы покрывают черновым отделочным слоем
, толщина которого составляет 150 мм. Процесс изготовления состоит из трамбовки жидкого бетона и вибропрессования, которое длится до 20 секунд.
Конструкционно-теплоизоляционный тип
Применяется для возведения несущих стен и ограждающих конструкций. Его плотность составляет от 500 до 800 кг/м 3 , в зависимости от марки. Конструкционное решение представлено блоками или жидким раствором, для возведения монолитных элементов здания.
Производители предлагают три типа конструкционно-теплоизоляционных блоков
:
- строительные, с черновым песчано-цементным внешним слоем и крепежными арматурными петлями;
- с добавлением отсева (шлаки, микрокремнезем);
- с облицовкой, с черновым слоем и декоративной отделкой под плитку, выполненной из песчано-цементной смеси или отделанные фасадной плиткой.
Черновой или декоративный слой защищают материал от атмосферных осадков, а также выступают в качестве пароизоляции.
Технические характеристики деревобетона не предполагают его использование в возведении фундамента.
Достоинства и недостатки материала
Благодаря высокой прочности на сжатие и изгиб, теплоизоляционным характеристикам и способности к хорошему звукопоглощению, деревобетон является одним из строительных материалов, которые отлично подходят для строительства частного дома
. Его небольшой вес не требует обустройства сложного фундамента, поэтому построить дом можно практически на любом грунте. Плюсом также является его низкая горючесть и отсутствие токсичности, при горении материала.
Большим преимуществом является низкая стоимость арболитовых блоков и наличие внешней декоративной отделки
. Это позволяет значительно сэкономить на утеплении и декоративном оформлении фасада. Обустройство простого фундамента также снижает расходы на строительство и значительно сокращает сроки возведения здания.
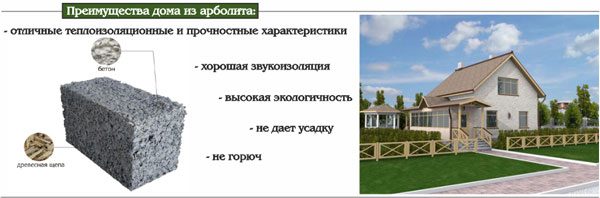
У легкого органического бетона есть ряд недостатков. Основной минус арболита – он продувается. Пористая структура бетона позволяет воздуху проникать в помещение, поэтому дом из арболита должен быть хорошо утеплен.
К минусам также относятся:
- высокий уровень водопоглощения делает нерациональным использование материала в помещениях с высокой влажностью или строительство в регионах с повышенным количеством атмосферных осадков;
- добавление химических присадок при изготовлении бетона снижают его экологичность;
- неровная поверхность блоков требует большего объема отделочных материалов.
Основные производители органического бетона
Чтобы минимизировать риски строительства из арболита, необходимо приобретать только качественный сертифицированный материал
. Есть несколько производителей, которые завоевали популярность на рынке строительных материалов:
- завод «Арболит-ЭКО» (Москва);
- сеть производственных цехов «Русский Арболит»;
- ОКБ «Сфера» (Иваново);
- Сибирский Арболит (Новосибирск).
Наличие собственного производства, оснащенного современными автоматизированными производственными линиями, позволяет выпускать материал с высокими качественными характеристиками. Производители предлагают доступные цены и удобные условия сотрудничества.
Арболит не является новым строительным материалом. Долгое время технология была забыта, в связи с приоритетом многоэтажного жилого строительства.
Сейчас его востребованность набирает обороты, поскольку материал удовлетворяет всем условиям, необходимым для возведения частного дома.
Полезное видео
Человек рассказывает про свой дом из арболита. Немного рекламирует фирму строителей, но суть не в этом.
По Арболиту
Арболит — его свойства и характеристики
Арболит
— (от лат. arbor — дерево и греч. lithos — камень), это строительный материал, разновидность лёгкого бетона. Изготовляется из высокосортного цемента и органических заполнителей (дроблёных отходов деревообработки, камыша, костры конопли и т. п). Нормативной базой для изготовления и применения арболита являются ГОСТ 19222-84 «Арболит и изделия из него. Общие технические условия» и СН 549-82 «ИНСТРУКЦИЯ по проектированию, изготовлению и применению конструкций и изделий из арболита».
1) Плотность.
Арболит в зависимости от средней плотности (объемной массы) в высушенном до постоянной массы состоянии подразделяют на:
теплоизоляционный — со средней плотностью до 500 кг/м3.
конструкционный — со средней плотностью свыше 500 до 850 кг/м3.
Примечание:
практика производства арболита показала, что при изготовлении арболита плотностью 500 кг/м3 достичь минимальной конструкционной прочности в 21 кгс/см2 очень и очень трудно (класс по прочности В 1,5). Такая прочность при плотности 500 кг/м3 получается только при изготовлении очень качественного арболита с применением чисто арболитовой щепы и абсолютном соблюдением технологии производства арболита без всяких отклонений от нее.
2) Прочность.
Показатель прочности арболита при сжатии характеризуют классами и марками:
В0,35; В0,75, В1 — для теплоизоляционного арболита.
В1,5; В2; В2,5; В3,5 — для конструкционного арболита.
М5, М10, М15 — для теплоизоляционного арболита.
М25, М35, М50 — для конструкционного арболита.
Примечание:
М25 = класс по прочности В1,5 — В2 (прочность на сжатие примерно 21-27 кгс/см2.);
М35 = класс по прочности В2,5 (прочность на сжатие примерно 34 кгс/см2.);
М50 = класс по прочности В3,5 (прочность на сжатие примерно 45 кгс/см2.);
Для строительства одноэтажного дома с мансардой или двухэтажного дома необходимо использовать конструкционный арболит с МИНИМАЛЬНОЙ маркой по прочности М25 = класс по прочности В1,5 (минимальная прочность на сжатие примерно 21 кгс/см2.)
3) Реальная теплопроводность арболита
, высушенного до постоянной массы, с заполнителем из древесины по результатам испытаний колеблется в следующих пределах:
Теплопроводность 0,08 Вт/м°C при плотности арболита 400-450 кг/м3.
Теплопроводность 0,09 Вт/м°C при плотности арболита 500 кг/м3.
Теплопроводность 0,11 Вт/м°C при плотности арболита 550 кг/м3.
Теплопроводность 0,12 Вт/м°C при плотности арболита 600 кг/м3.
Теплопроводность 0,13 Вт/м°C при плотности арболита 650 кг/м3.
Теплопроводность 0,14 Вт/м°C при плотности арболита 700 кг/м3.
4) Морозостойкость.
«Морозостойкость строительных материалов — это способность материалов в увлажнённом состоянии выдерживать без разрушения многократное замораживание, чередующееся с оттаиванием. Основная причина разрушения материала под действием низких температур — расширение воды, заполняющей поры материала, при замерзании. Морозостойкость зависит главным образом от структуры материала: чем выше относительный объём пор, доступных для проникновения воды, тем ниже морозостойкость.
Повышение морозостойкости стройматериала достигается путём снижения его водопоглощения, например за счёт увеличения доли закрытых пор, повышения плотности наружных слоев материала, или гидрофобизацией его поверхности». (Большая Советская Энциклопедия).
Морозостойкость арболита 25-50 циклов полного замораживания и полного оттаивания замороженного материала. Учитывая низкую сорбционную влажность арболита, защита арболита штукатурным слоем в 2 см. или иным видом внешней отделки, снижающим водопоглощение арболита, является эффективным способом предотвращения появления полноценных циклов замораживания-оттаивания и значительно увеличивает срок использования арболита. При этом есть достаточно много примеров эксплуатации домов и бань из арболита (7-10 лет) не имеющих с внешней стороны никакой отделки без негативных последствий для стен. Но надо знать, что отсутствие внешней штукатурки или затирки увеличивает продуваемость стен и увеличивает теплопотери.
Регистрация:
06.03.08
Сообщения:
27.204
Благодарности:
29.814
5) Влагопоглощение.
Арболит имеет пористую структуру и объем межзерновых пустот арболита в соответствии с ГОСТ 19222-84 «Арболит и изделия из него. Общие технические условия» не нормируется. Все это приводит к тому, что арболит, основным заполнителем которого является древесная щепа, имеет высокое влагопоглощение. Что это означает? Это значит, что блок арболита, находящийся в воде в состоянии поглотить (впитать в себя) воду в размере 40-80% от своего объема. Но, несмотря на это, арболит является негигроскопичным материалом и имеет очень низкую гигроскопичность (сорбционную влажность)
. Гигроскопичность (сорбционная влажность) — это свойство капилярно-пористого материала поглощать водяной пар из окружающей воздушной среды. Т. е. арболит, находящийся в естественных условиях, на улице, в стене дома, фактически не накапливает в себе влагу, т. к. благодаря очень низкой сорбционной влажности материала он почти не впитывает влагу из воздуха. Это качество арболита позволяет избегать влагонасыщения стен при условии отсутствия с внешней стороны стены пароизоляции или паронепроницаемого материала. Внешняя отделка домов штукатуркой с финишным слоем из паропроницаемых материалов, имитацией бруса или блокхаусом, сайдингом, облицовочным кирпичом с вентилируемым воздушным зазором, любым видом вентилируемых фасадов в максимальной степени соответствует свойствам арболита. Более того, практика использования арболита в качестве материала для строительства бань показала, что арболитовые бани, не имеющие никакой внешней отделки по стенам находятся в прекрасном состоянии. Несмотря на это, целесообразно устраивать внешнюю защиту стен из арболита в период до трех лет после строительства дома, хоз. помещения, гаража или бани с целью снижения влагопоглощения арболита и соответственно повышения морозостойкости и долговечности конструкции.
6) Усадка и усушка.
Необходимо различать эти два понятия.Усушка (потеря веса, без потери объема).
Согласно ГОСТ 19222-84 п.
1.2.8. «Влажность арболита в изделиях при отгрузке их потребителю не должна превышать 25% по массе». Практика показывает, что усушка качественного арболита по весу (т.е. потеря веса от испарения влаги, находящейся в блоке), не ведет к потере прочности арболита и к увеличению усадки. Т. е. в зависимости от того, какая отпускная влажность у блоков, арболит может высохнуть на большее или меньшее количество килограмм. Потеря веса в первую очередь зависит от количества влаги в блоке, от плотности трамбовки (уплотнения) блока и от количества цемента. Конструкционный арболит начинается с плотности в 500 кг/м3 в высушенном до постоянной массы состоянии. Поэтому, в договорах на покупку арболита необходимо предусмотреть пункт о том, что покупаемый вами арболит является конструкционным (предназначен для строительства несущих и самоненесущих стен дома) и по средней плотности (объемной массы) в высушенном до постоянной массы состоянии должен соответствовать ГОСТ 19222-84
п. 1.2.1., т. е. весить более 500 кг/м3. Если вам необходим арболит в высушенном до постоянной массы состоянии с плотностью более чем 500 кг/м3, то этот момент надо обязательно отражать в договорах. При этом необходимо помнить, что на способность материала нести нагрузки влияет не плотность материала, а его прочность.
P. S. При монолитной заливке арболитовой смеси в опалубку, а также при использовании крупноформатных плит с размерами не менее 3,4 м. в длину, 2,6 м. в высоту и 0,4 м. в ширину в качестве несущих стену дома можно использовать арболит с плотностью от 300 кг/м3 и выше. Прочностные характеристики стены дома из такого массива арболита примерно соответствуют прочности кладки стены из мелкоштучных блоков арболита с весом 500-550 кг/м3.
Усадка
(потеря веса, с потерей объема).
Арболит имеет очень маленькую усадку, в пределах 0,1-0,4 % в зависимости от качества блока. Т. к. большинство производителей арболита применяет при производстве способ немедленной распалубки форм, то блоки арболита после изготовления не содержат большого количества избыточной влаги. Практика применения и использования арболита показала, что в блоке, находящемся на складе или на строительной площадке, усадочные процессы самого блока полностью прекращаются через 1,5-2 месяца после производства. При строительстве домов из арболита, особенно 2х этажных с железобетонными плитами перекрытий, небольшие усадочные явления под нагрузкой все таки присутствуют, но по большей части это усадка не самого материала, а в целом стен, в том числе и усадка кладочного раствора под нагрузкой. Практика показала, что штукатурку по арболиту можно использовать где-то через 4 месяца после производства блока, НО НЕ РАНЕЕ чем через полтора — два месяца после окончания строительства коробки дома под крышу.
- Регистрация:
06.03.08
Сообщения:
27.204
Благодарности:
29.814
Производство арболита
Часть 1. Компоненты арболита
Для тех, кто решил самостоятельно организовать производство арболита, необходимо начать с изучения работ Наназашвили И. Х., в частности его книги «Арболит — эффективный строительный материал». М., Стройиздат, 1984. Эта книга есть в электронном виде: http://www.stroytechnolog.ru/books/arbolit1.html Также необходимо изучить ГОСТ 19222-84 «Арболит и изделия из него. Общие технические условия» и СН 549-82 «Инструкция по проектированию, изготовлению и применению конструкций и изделий из арболита»
Для того, чтобы получить качественный арболит необходимо понимать, что производство арболита кардинально отличается от производства всех других видов бетонов, как легких (полистиролбетон, керамзитобетон), так и ячеистых (газобетон и пенобетон).
Компоненты арболита:
1) древесная щепа.
2) цемент.
3) минерализаторы.
4) вода.
Несмотря на небольшое количество компонентов и кажущуюся простоту изготовления, производство арболита является трудоемким процессом в виду того, что щепа и цемент по своей природе не сцепляются друг с другом. И для того, чтобы получить единый материал (арболит-щепобетон), необходимо соблюсти целый ряд технологических моментов, иначе у вас не получится арболит. При этом надо понимать, что в данном разделе речь идет о получении качественного арболита, который соответствует всем требованиям ГОСТ 19222-84.
! ВАЖНО:
производство арболита в холодное время года возможно при стабильной круглосуточной температуре внутри помещения не ниже +12+15 градусов. При более низкой температуре возникает проблема с гидратацией цемента и соответственно с качеством блока.
! ВАЖНО:
круглогодичное производство арболита требует наличие оборотного капитала, который позволит производить арболит в течение минимум 2-3 месяцев в период, когда спрос либо отсутствует полностью, либо минимален.
ЩЕПА ПОД АРБОЛИТ (часть 1)
Щепа (вид леса)
. Для получения качественного арболита наилучшим образом подходит щепа хвойных пород, в первую очередь сосны и ели. Согласно ГОСТ 19222-84 п.
1.4.2. «В качестве органических заполнителей должны применяться: измельченная древесина из отходов лесозаготовок, лесопиления и деревообработки хвойных (ель, сосна, пихта) и лиственных (береза, осина, бук, тополь) пород, костра конопли и льна, измельченные стебли хлопчатника и измельченная рисовая солома.» Также арболит можно изготавливать на основе щепы лиственницы. Но использование щепы лиственницы требует кардинального увеличения объемов хим. добавок на обработку щепы, как минимум в 2 раза по сравнению с сосной.
Щепа (форма щепы).
Для изготовления арболита щепа должна быть определенной формы. Согласно ГОСТ 19222-84 п.
1.4.3. «Органические заполнители должны удовлетворять следующим требованиям:
а)
измельченная древесина:
— размеры древесных частиц не должны превышать по длине 40, по ширине 10, а по толщине5 мм;
— содержание примеси коры в измельченной древесине не должно быть более 10%, а хвои и листьев более 5% по массе к сухой смеси заполнителей;
б)
костра конопли и льна, измельченные стебли хлопчатника и измельченная рисовая солома:
длина частиц не должна быть более40 мм;
содержание очесов и пакли не должно быть более 5% от массы сухой смеси заполнителя.
Измельченная древесина, костра конопли и льна, измельченные стебли хлопчатника и рисовой соломы не должны иметь видимых признаков плесени и гнили, а также примеси инородных материалов (кусков глины, растительного слоя почвы, камней, песка и пр.), а в зимнее время примесей льда или снега.»
Но многочисленные исследования, проведенные в Советском Союзе по изучению арболита показали, что самой идеальной формой арболитовой щепы является следующая форма по размерам: «Древесина — анизотропный материал, поэтому древесная дробленка должна иметь игольчатую форму с коэффициентом формы (отношение наибольшего размера к наименьшему), равным 5-10, толщину 3-5 мм и максимальную длину до 25 мм.
Частицы такой формы обладают более близкими по абсолютному значению влажностными деформациями вдоль и поперек волокон, и поэтому в отличие от заполнителя с меньшим коэффициентом формы могут снизить отрицательное воздействие влажностных деформаций древесного заполнителя на структурообразование и прочность арболита.»
Лучшие результаты дает специально приготовленная дробленка из кусковых отходов древесины дровяного сырья, получаемая по типовой двухступенчатой схеме: получение щепы на рубительных машинах, а затем измельчение щепы и ее гомогенизация в молотковых мельницах.
- Регистрация:
06.03.08
Сообщения:
27.204
Благодарности:
29.814
ЩЕПА ПОД АРБОЛИТ (часть 2).
То, что требует ГОСТ и то, какой должна быть щепа по результатам исследований Наназашвили понятно. А что есть в реальности? Где взять щепу необходимых размеров или на каких дробилках ее получить — вопрос очень важный для производителей арболита, фактически это вопрос №1. Этот вопрос остается важным и для тех, кто только задумывается о производстве арболита.
Вот некоторые пояснения по щеподробилкам и щепе.
Основная масса рубительных машин по дроблению деревоотходов предназначена для получения технологической щепы. Щепа технологическая должна соответствовать ГОСТ 15815-83 ЩЕПА ТЕХНОЛОГИЧЕСКАЯ ТЕХНИЧЕСКИЕ УСЛОВИЯ. Данный ГОСТ предполагает достаточно широкий разброс размеров щепы, а главное, он не регламентирует ШИРИНУ щепы. Т. е. в нормах длина и толщина. Все это привело к тому, что основная масса щеподробилок, производящих технологическую щепу делают ее шириной 2,5 см. И если длина или толщина как-то регулируются, то ширина почти нет. Поэтому основная масса рубилок делает технологическую щепу ромбиками или прямоугольниками с размерами близкими к 2х3 см. Из такой щепы можно делать только теплоизоляционный арболит, и я уверен, что его характеристики, будут значительно хуже, чем у арболита, сделанного из специальной щепы. Но раз технологическая щепа фактически не подходит (или подходит мало), то где взять нужную щепу?
На сегодняшний момент есть на мой взгляд несколько вариантов:
1) Двухступенчатая схема: получение технологической щепы на дисковых рубительных машинах (или поеупка такой щепы отдельно), а затем измельчение технологической щепы и ее гомогенизация в молотковых мельницах или на молотковых дробилках.
Этот вариант является основным и рекомендован к производству арболитовой щепы. Для производства технологической щепы можно использовать весь спектр дисковых дробилок, которых достаточно много, как российских, так и импортных. С молотковыми дробилками проблема более серьезная, но на сегодняшний момент есть вариант молотковой дробилки украинского производства. В качестве примера можно посмотреть этот вариант у фирмы СОГАЛ-ЭКО http://www.sogal-eco.ru/oborudbriket.html Изначально такие дробилки настроены на изготовление мелкой щепы для производства топливных брикетов (размер щепы 12х2х2 мм.). Но у таких дробилок есть возможность изменить параметры дробления путем снижения оборотов двигателя и изменением размера сита.
ВАЖНО:
специальных молотковых дробилок для дробления технологической щепы в продаже очень мало, но принцип их работы несложный и при наличии инженера-конструктора можно самостоятельно изготовить молотковую дробилку, в которой будет дробится технологическая щепа. Опыт производителя арболита из Иркутска свидетельствует о том, что это возможно.
2)
Дисковые рубительные машины с регулируемыми ножами.
На таких рубилках делают технологическую щепу. Но некоторые рубилки можно настроить таким образом, что размер щепы изменится. Такой, как положено для арболита она конечно не станет, но тем не менее, возможно получение более узкой и короткой щепы. Но узнать, можно ли настроить такую дробилку и какую щепу она в итоге выдаст обычно реально только после покупки. Так что с такими дробилками есть некоторый вариант попасть на щепу немного не с теми размерами, которые нужны, поэтому если производить арболит (щепобетон) на щепе из под дисковой дробилки, то безусловно необходимо посмотреть ту щепу, которую она выдает. Ниже фотка дробилки ДОС-1 и щепа из под нее.
А вот так выглядит технологическая щепа с дисковых рубительных машин, когда такие машины настроены на получение такой технологической щепы.
3)
Щепа (стружка) с калибровочных станков.
Есть станки, которые калибруют бревна и при срезе с них стружки или щепы необходимо настроить эти станки так, чтобы срезы были не толстыми, а 4-5 мм. толщиной. При таких срезах щепа получается очень близкой по размерам к требованиям арболитового ГОСТа. Производителям бревен такой вариант срезки невыгоден, но технически такая срезка возможна, правда как я понял не на всех станках. Такая щепа (стружка), если ее размеры близки к необходимым и она не очень широкая вполне подойдет для производства арболита, но нужны испытания конечного результата на прочность. Видел арболит (щепобетон) сделанный на такой щепе, в принципе по прочности достаточно хороший вариант. По геометрии есть небольшие погрешности, которые можно устранить путем повышения контроля за производством и применением либо станков, либо несъемной опалубки.
4)
Щепа с роторно-ножевых дробилок.
На таких дробилках делают топливную щепу, т. е. более тонкую и менее широкую. Этот вариант чисто арболитовой щепы, так как щепа с таких дробилок не превышает по толщине и ширине 0,5 см., а длина на таких дробилках регулируется. НО! У таких дробилок есть два определенных минуса или скажем так момента, которые надо иметь ввиду:
а) на роторах стоит достаточно большое количество ножей, которые при регулярной работе требуют либо замены, либо наплавки (их не точат). Это доп. затраты.
б) для таких дробилок ограничен размер используемого сырья. деревоотходы для таких дробилок должны не превышать размеры 10х10х45 см. (для небольшой и средней по производительности дробилки). так что для таких дробилок деревоотходы надо изначально готовить.
А вот так выглядит поверхность блока арболита, сделанного из щепы, изготовленной на роторно-ножевой дробилке
ОЛНОВА DP 660 P. Такая щепа делалась путем одного перемола, т. е. горбыль резался на отрезки длиной до 40 см. на циркулярке, а потом такие отрезки закладывались в роторно-ножевую дробилку
ОЛНОВА DP 660 P. Щепа на выходе получается арболитовая.
ВАЖНО:
такие дробилки мож
но использовать не только в качестве первого перемола деревоотходов, но и в качестве дробилок второго помола, когда в них дробятся не деревоотходы, а технологическая щепа. После дробления технологической щепы получаются достаточно мелкие щепки, хорошо пригодные для производства арболита. Примером роторно-ножевой дробилки является вариант ОЛНОВА DP 660Pукраинского производства.
5)
Валковые измельчители (шредеры).
Они выдают такую щепу, какую надо. Т. е. они изготавливаются под конкретный тип щепы и производят только его. На них можно делать чисто арболитовую щепу. Выход фракции щепы заданных размеров не ниже 85%. Минусы шредеров:
а) в России их почти не производят. Есть несколько заводов, которые их изготавливают, но там делают достаточно большие по объему шредеры с ценами от 800 тысяч рублей при наличии 100% предоплаты и специального заказа, т. к. типовые шредеры начинаются с суммы в 1,5 млн. рублей и обладают очень большой производительностью, которая не всегда нужна производителям арболита. Для небольших арболитовых производств, особенно для начинающих, это конечно очень дорого. Но при расширении производств — это хороший вариант.
б) на российских шредерах как я понял нет ограничений по размерам деревоотходов (до разумных пределов конечно), просто чем меньше нужна щепа, и чем больше вы будете класть деревоотходы по размерам, тем ниже будет производительность. Вот и все. Это не минус, но тем не менее доп. расходы. К слову, шредеры перемалывают все, что можно: камень, бетон, железо и т. д. Их валы делают из специальной стали и при использовании для измельчения деревоотходов их не надо будет точить.
в) на немецких шредерах установлен комплект ножей, который требует замены после определенного количества часов работы, а это тоже затраты.
Вот так выглядит щепа с российских валковых измельчителей (шредеров).
- Регистрация:
06.03.08
Сообщения:
27.204
Благодарности:
29.814
Цемент.
Для производства арболита желательно использовать высокомарочные цементы, как минимум от М400 и выше. Самым оптимальным решением на данный момент по соотношению цена-качество является использование цемента марки М500 и выше. При использовании цемента надо обязательно иметь ввиду, что его характеристики будут меньше заявленных производителем. На данный момент марка цемента большинства поставщиков и производителей не соответствует заявленной и регулярно оказывается ниже, как минимум на 40-50 единиц. При этом достаточно часто встречаются случаи, когда покупая цемент М500, вы фактически покупаете цемент М400. Все это надо иметь в виду при расчетах объемов цемента.
Согласно СН 549-82 «Инструкция по проектированию, изготовлению и применению конструкций и изделий из арболита» п. 2.2. Вяжущие должны удовлетворять требованиям следующих стандартов:
портландцемент и быстротвердеющий портландцемент ГОСТ 10178
–
76;
цемент сульфатостойкий ГОСТ 22266
–
76;
портландцемент белый ГОСТ 965
–
78;
портландцемент цветной ГОСТ 15825
–
80.
3) Хим. добавки.
Как говорилось уже выше, щепа и цемент не сцепляются друг с другом без предварительной обработки щепы хим. добавками. Такая обработка необходима для того, чтобы устранить из щепы сахара, которые препятствуют сцеплению щепы и цемента, а также для ускорения твердения арболита. Список возможных хим. добавок для устранения сахаров и ускорения твердения арболита приведен в СН 549-82 «Инструкция по проектированию, изготовлению и применению конструкций и изделий из арболита»:
2.13. Химические добавки для арболитовой массы должны удовлетворять требованиям следующих стандартов:
хлорид кальция ГОСТ 450
–
77;
жидкое стекло ГОСТ 13078
–
67;
силикат-глыба ГОСТ 13079
–
67;
сернокислый глинозем ГОСТ 5155
–
74;
окись кальция (известь) ГОСТ 9179
–
77.
Допускается введение порообразующих добавок, используемых при производстве поризованных легких бетонов, а также других химических добавок, в том числе комплексных, после лабораторной проверки по согласованию с базовой организацией – НИИЖБ Госстроя СССР.
2.14. Химические добавки для арболитовой массы применяются в виде водных растворов требуемой плотности как в отдельности, так и в сочетании друг с другом. Плотность замеряется денсиметром.
2.15. Жидкое стекло должно иметь модуль от 2,4 до 3. Модуль жидкого стекла определяется по ГОСТ 13078–67. Для быстрой предварительной оценки модуля жидкого стекла может быть применен полевой способ согласно Инструкции по технологии приготовления жаростойкого бетона.
Реальное практическое применение хим. добавок показало, что сейчас для производства арболита в основном используется либо хлорид кальция
(как самостоятельно, так и в сочетании с жидким стеклом),
либо сернокислый глинозем
(как самостоятельно, так и в сочетании с известью).
Хим. добавки вводятся в состав арболитовой смеси исключительно в виде водных растворов, т. е. после предварительного замачивания и растворения в воде.
4) Вода.
Согласно ГОСТ 19222-84 п. 1.4.7. Вода для приготовления арболита должна соответствовать требованиям ГОСТ 23732-79. Нна практике для производства арболита используют ту воду, которая доступна: из центрального водопровода, из колодцев и скважин. Серьезным моментом при использовании воды, на который следует обратить внимание. является температура воды, а точнее температура водного раствора с хим. добавками, который добавляется в смеситель при изготовлении арболита. Температура воды очень сильно влияет на быстроту гидратации (схватывания) цемента, которая наиболее эффективна при температуре воды от 15 градусов и выше. При температуре воды меньше 7-8 градусов скорость гидратации цемента падает очень резко, т. е. гидратация цемента почти не происходит. Именно поэтому в замес нужно заливать водный раствор с температурой хотя бы 12-15 градусов.
Как получить водный раствор с хим. добавками такой температуры каждый решает сам: либо небольшой подогрев, либо заливание воды в емкости заранее, чтобы ее температура успела подняться до требуемой. При этом надо иметь ввиду, что применение в качестве хим. добавки хлористого кальция в сухом состоянии автоматически увеличивает температуру водного раствора до требуемой вследствие реакции воды и хлористого кальция.
- Регистрация:
06.03.08
Сообщения:
27.204
Благодарности:
29.814
Производство арболита.
Часть 2. Способы производства арболита.
В Советском Союзе производство арболита было распространено очень широко и основными способами
уплотнения арболитовой смеси были: циклическое прессование (немедленная распалубка), вибрирование с пригрузом (немедленная распалубка), вибропрессование с фиксирующей крышкой, силовой вибропрокат, послойная укладка и уплотнение и др. Каждый из этих способов имеет как преимущества, так и недостатки. Критерий оценки оптимальности уплотненной структуры следующий: чем оптимальнее уплотненна структура арболита, тем меньшими должны быть давление набухания и относительная величина деформации набухания. При виброуплотнении с пригрузом частицы древесного заполнителя, перемещаясь одна относительно другой, занимают в структуре арболита оптимальное положение, обеспечивающее наибольшую площадь контактных зон; при этом уменьшается редеформация — распрессовка. При обычном же способе прессования арболитовой смеси для получения изделий одинаковой средней плотности частицы древесного заполнителя сжимаются, вызывая упругие деформации, что ведет к распрессовке отформованного изделия и, в конечном итоге, к снижению конечной прочности. Т. е., для получения арболитовых изделий одинаковой средней плотности при уплотнении арболитовой смеси обычным прессованием необходимо приложить усилие в 10-20 раз больше, чем при прессовании вибропригрузом (причем эти усилия необходимо фиксировать жесткой крышкой, что связано с увеличением металлоемкости оснастки). Поэтому обычное прессование практически не используется для изготовления арболита, так как затраты и трудоемкость процесса при изготовлении таким способом выше.
Производство арболита с помощью циклического прессования является очень эффективным способом производства арболита, но оно не получило распространение в связи со значительным увеличением времени, необходимого на изготовление (формирование) блока.
Справка:
Пособие к СНиП 3.09.01-85 Пособие по технологии формования железобетонных изделий п. 7.10. Прессование может производиться в статическом или циклическом режимах. Статическое прессование предполагает одноразовое приложение нагрузки к смеси и выдерживание под ней до стабилизации деформаций, циклическое прессование — многократное приложение и снятие нагрузки с определенной периодичностью. При циклическом прессовании величина формующего давления может быть в 50 — 100 раз меньше, чем при статическом. Статическое прессование применяют для смесей любой консистенции, при давлении 3…10 МПа.
Для конструкционного арболита при толщине 150-200 мм. удельное давление равно 0,7- 0,8 МПа. Режим уплотнения такой: сжатие арболитовой смеси и выдерживание при постоянной деформации — 30 с, снижение усилия прессования до нуля, выдерживание без давления — 15 с, затем давление прессования восстанавливают до первоначального значения. Цикл повторяется три раза. На практике время изготовления арболита таким способом оказалось очень большим и данный способ будет экономически выгодным только при одновременном изготовлении большого количества блоков, от 5-6 шт. за раз.
Сейчас применяют в основном несколько видов производства арболита:
1) арболит с использованием ручной трамбовки на полу помещения.
2) арболит с использованием ручной трамбовки на вибростоле.
3) арболит на вибростанке.
4) арболит на станке вибрирование с пригрузом.
- Регистрация:
06.03.08
Сообщения:
27.204
Благодарности:
29.814
Производство арболита.
Часть 3. Оборудование для производства арболита различными способами.
1) Производство арболита с помощью ручной трамбовки на полу помещения.
Это самый экономичный с точки зрения затрат при открытии предприятия способ производства арболита. Необходимо иметь смеситель принудительного типа; емкость, в которой будут разбавляться хим. добавки; мерные емкости, которыми будут в смеситель засыпаться цемент и щепа; стальные формы, в которых будет производится трамбовка арболита; тележку, на которой от смесителя арболитовая смесь будет подвозиться к формам; ровную поверхность, на которой будет происходит формирование блока (бетонный пол, фанера, поддон с фанерной поверхностью); поддоны, на которые будет складываться готовый арболит.
Процесс производства арболитового блока с помощью ручной трамбовки на полу помещения:
1) В емкости с водой заранее разбавляются хим. добавки, например хлористый кальций или сернокислый алюминий из расчета 10-12 кг/м3 арболита (для лиственницы в 2 раза больше). Перед использованием надо раствор перемешать.
ВАЖНО:
хим. добавка на основе сернокислого алюминия может быть комплексной. Т. е. 8 кг. сернокислого алюминия на 1м3 арболита и 4 кг. извести на м3 арболита. В случае использования и сернокислого алюминия и извести, приготовление хим. растворов этих минерализаторов надо осуществлять в отдельных емкостях. Этот вариант лучше, чем просто сернокислый алюминий.
2) В смеситель засыпается щепа. Практика показывает, что принудительным смесителям типа РН-300 и им подобным очень тяжело перемешивать заявленный производителем объем. Реально в РН-300 можно засыпать не больше 150 литров щепы. Объем щепы зависит от ее размера.
3) Запускается смеситель и в процессе перемешивания щепы заливается водный раствор хим. добавок. Если есть возможность распыления этого водного раствора – хорошо. Если нет, то задача при заливке водного раствора состоит в том, чтобы вылить раствор максимально равномерно по всему объему щепы. Т. е. чтобы при заливке раствора намокло как можно больше щепы. Если воду вылить с одной стороны смесителя, то есть вероятность того, что в процессе перемешивания не вся щепа увлажнится. Перемешивание длится минимум 10-20 секунд и после этого засыпается цемент.
4) Цемент засыпается таким образом, чтобы покрыть цементным тестом максимальное количество площади щепок. В идеале 100%. После засыпки цемента перемешивание длится минимум 3 минуты.
ВАЖНО:
ВАЖНО:
мало воды тоже плохо, потому что вода – это необходимая составляющая для гидратации цемента и если воды будет мало, цемент может не набрать необходимую прочность. На количество воды также влияет влажность щепы, поэтому количество воды определяется опытным путем.
6) При укладке смеси в формы желательно осуществлять штыкование смеси узкими вилами и только потом притрамбовывать. Надо понимать, что сильная прессовка смеси ничего не даст и смесь просто будет возвращаться в исходное состояние. Именно поэтому важно смесь при укладке постоянно осаживать вилами, а потом просто притрамбовывать стальной трамбовкой.
7) Блоки можно переносить через 2-3 дня в зависимости от влажности воздуха в помещении. Складывать блоки один на другой желательно не раньше чем через 3-4 дня. Складывать блоки в 3 ряда в высоту и больше желательно не раньше чем через 6-7 дней после изготовления.
8) Транспортировать блоки можно через 15-20 дней после изготовления при сухой погоде и не ранее чем через 20 дней при сырой погоде.
ВАЖНО:
производство ручным способом позволяет использовать всего несколько форм (на 1-2 блока каждая) и осуществлять мгновенную распалубовку блоков, т. е сразу после того, как произвели трамбовку. Но если ручные формы сделать на 6-8-10 блоков и оставлять блоки после трамбовки в таких формах хотя бы на 10-12 часов, то этот вариант будет безусловно лучше мгновенной распалубовки по нескольким причинам: 1) в этом варианте для гидратации цемента будет больше воды, которая испаряется намного медленнее, чем при мгновенной распаковке форм, т. к. борта формы не снимаются долгое время. 2) отсутствие воздействия на стенки блока и на сам блок в первые 10-12 часов после изготовления позволяют создать более прочный конгломерат цемент-древесина.
Плюсом
этого варианта является отсутствие станка, поддонов и стеллажей для хранения блоков.
Минусом
этого варианта является необходимость наличия больших площадей производственного помещения и постоянно разная плотность блоков (правда минимальная прочность таких блоков всегда достаточна для строительства, просто может быть некий перерасход арболитовой смеси при более плотной утрамбовке).
- Регистрация:
06.03.08
Сообщения:
27.204
Благодарности:
29.814
2) Производство арболита с использованием ручной трамбовки на вибростоле.
Это вариант является более затратным способом производства арболита с точки зрения затрат при открытии предприятия. Необходимо иметь смеситель принудительного типа; емкость, в которой будут разбавляться хим. добавки; мерные емкости, которыми будут в смеситель засыпаться цемент и щепа; тележку, на которой от смесителя арболитовая смесь будет подвозиться к вибростолу; вибростол; небольшие поддоны из фанеры или стали на 1-2 блока, на которых будет происходить формование блока; стальные формы; стеллажи для складирования поддонов с изготовленным арболитом; деревянные поддоны, на которые будет складываться готовый арболит.
Процесс производства арболитового блока
на вибростоле:
ВАЖНО:
P
.
S
ВАЖНО:
после того, как в смеситель засыпан цемент, воду в смеситель уже добавлять нежелательно, так как вода смоет со щепок цементное тесто и это может привести к снижению прочности блоков.
5) Смесь после изготовления живет реально 10-15 минут, т. е. за это время смесь надо уложить в формы и утрамбовать. Консистенция смеси может быть разной. Если распалубовка блоков немедленная, т. е. сразу после трамбовки, то смесь должна быть с минимально необходимым объемом воды. Если распалубовка через сутки, то воды можно побольше.
способ производства арболита мало воды тоже плохо, потому что вода – это необходимая составляющая для гидратации цемента и если воды будет мало, цемент может не набрать необходимую прочность. На количество воды также влияет влажность щепы, поэтому количество воды определяется опытным путем.
6) На вибростол ставится поддон со стальной формой под блок. Туда закидывается смесь и проштыковывается. Затем включается вибростол на 10-20-30 сек. (в зависимости от консистенции смеси и необходимой прочности.) Время вибрирования устанавливается опытным путем. После вибрирования поддон с формой, в которой проштыкованная и провибированная смесь снимается и утрамбовывется. Возможны варианты утрамбовки прямо на вибростоле, но эти варианты проверяются опытным путем.
ВАЖНО:
при укладке смеси в формы желательно осуществлять штыкование смеси узкими вилами и только потом притрамбовывать. Надо понимать, что сильная прессовка смеси ничего не даст и смесь просто будет возвращаться в исходное состояние. Именно поэтому важно смесь при укладке постоянно осаживать вилами, а потом просто притрамбовывать стальной трамбовкой.
ВАЖНО:
вибрирование арболитовой смеси длительное время негативно сказывается на качестве смеси, т. к. при длительном вибрировании значительная часть цементного теста слезает с щепок и стекает вниз. Именно поэтому желательно перед вибрированием проштыковать смесь, таким образом уже ее уплотнив. Определение времени вибрирования должно происходить именно с учетом данного факта.
ВАЖНО:
дляизготовления конструкционного арболита плотностью от 500 кг/м3 и вышеобщая утрамбовка насыпной смеси должна быть не менее 25%.
Т. е., если высота блока 20 см., то высота формы должна быть не менее 25 см. и эти лишние 5 см. будут утрамбованы. Если высота формы будет выше высоты блока не на 5 см., а на 8-10 см., то плотность блока вырастет не менее чем на 80-100 кг., а соответственно вместе с плотностью вырастет и прочность.
7) После изготовления блока поддон с блоком переносится на стеллаж. В зависимости от консистенции полученного арболита, поддон может переносится либо со стальной формой (и потом форма будет сниматься), либо без формы. Данный момент также устанавливается опытным путем.
ВАЖНО:
на разных производствах сроки отгрузки могут отличаться и они зависят от большого количества факторов, начиная с марки и качества цемента и до влажностного режима в помещении и условиях уличного хранения.
ВАЖНО:
Коэффициент уплотнения назначается в зависимости от требуемой средней плотности арболита и составляет 1,2-1,6. Для средней плотности 700 кг/мЗ при использовании дробленки хвойных пород он равен 1,5.
Плюсом
этого варианта является отсутствие станка как такового и соответственно более низкие капитальные затраты на открытие производства; более высокая однородность блоков, что увеличивает получение блоков одной и то же плотности; возможность иметь не очень большое по площади помещение, т. к. на стеллажах блоки можно ставить в 5-7 рядов.
Минусом
этого варианта является необходимость наличия большого количества поддонов под каждый блок, т. к. их надо не менее 3х дневных смен. Также к минусам можно отнести необходимость наличия стеллажей.
- Регистрация:
06.03.08
Сообщения:
27.204
Благодарности:
29.814
3) Производство арболита на вибростанке.
Это вариант является достаточно затратным способом производства арболита с точки зрения затрат при открытии предприятия. Необходимо иметь смеситель принудительного типа; емкость, в которой будут разбавляться хим. добавки; мерные емкости, которыми будут в смеситель засыпаться цемент и щепа; тележку, на которой от смесителя арболитовая смесь будет подвозиться к вибростолу; вибростанок; небольшие поддоны из фанеры или стали на 1-2 блока, на которых будет происходить формование блока; стальные формы; стеллажи для складирования поддонов с изготовленным арболитом; деревянные поддоны, на которые будет складываться готовый арболит; тележка, на которой готовые блоки будут отвозиться к стеллажам (в зависимости от организации процесса может не понадобиться).
ВАЖНО:
на рынке продается огромное количество разных вибростанков, но к сожалению без внесения изменений, практически ни один из них не пригоден для производства арболита. Это в первую очередь связано с процессом вибрирования. Если при производстве арболита на вибростоле происходит штыкование (т.е. предварительное уплотнение смеси, которое не дает возможности цементному тесту стекать вниз), то при производстве арболита на обычном вибростанке процесса штыкования смеси нет. И если например вибрировать смесь по времени минуту-две, то после такого вибрирования большая часть цементного молочка с щепок стечет вниз.
ВАЖНО:
Вот так описан способ производства арболита вибропрессованием,
где упругая смесь сжата крышкой формы до набора распалубочной прочности,
на одном из производств арболита в СССР.
Способ вибропрессования
разработан ЦНИИМЭ и внедрен впервые в Шеманихинском леспромхозе Горьковской области. В настоящее время по такому способу в модернизированном исполнении работают две линии формования арболитовых конструкций в Оятской сплавной конторе Ленинградской области (линии ЛВ-24М и ЛВ-125М). Изготовление арболитовых изделий осуществляется в стальных формах с фиксирующими крышками. Форма с уложенными фактурными слоями и арболитом, арматурой и закладными деталями накрывается фиксирующейся крышкой и подается на тележке в вибропрессовальную установку; под действием вибрации и сжатия гидродомкратов крышка утапливается в форму, уплотняет смесь и защелкивается.
Изделие в форме с зафиксированной крышкой выдерживается в отапливаемом цехе до достижения распалубочной прочности. Этим способом могут быть получены изделия хорошего качества с любой требуемой средней плотностью. Недостатки его — большой расход металла на формы и крышки, поскольку для сдерживания давления распрессовки упругой арболитовой смеси, находящейся в напряженно сжатом состоянии, требуется большая жесткость форм и крышек. Гидравлические домкраты при работе находятся под вибрацией, что снижает срок их службы. Такие недостатки препятствуют широкому внедрению этого способа.
Таким образом, чтобы использовать вибростанки для производства арболита, надо сделать такую конструкцию, которая бы исключала бы использование стальных форм с закрывающейся крышкой. Т. е. блок после прессования должен подаваться на сушку сразу уже в распакованном виде. Чтобы этого достичь, в обычный вибростанок необходимо внести изменения.
ВАЖНО:
изменения в обычный вибростанок вносятся по двум направлениям:
а)
в части процесса вибрирования, чтобы кардинально сократить время этого процесса хотя бы до 10-15 секунд. Здесь взамен виброплощадки обычного типа, более целесообразно применение виброударной установки.
б)
усилие, осуществляемое прессом. Если для статического прессования смеси в форме (однократное приложение нагрузки),
где упругая смесь сжата крышкой формы до набора распалубочной прочности (20-24 часа)
достаточно приложение усилий 0,35 мПа, то для обычного прессования с мгновенной распалубовкой усилие должно быть не менее 2-3 мПа.
Не все вибростанки имеют такое усилие.
Процесс производства арболитового блока с помощью вибростанка:
1) В емкости с водой заранее разбавляются хим. добавки, например хлористый кальций или сернокислый алюминий из расчета 10-12 кг/м3 арболита (для лиственницы в 2 раза больше). Перед использованием надо раствор перемешать.
ВАЖНО:
хим. добавка на основе сернокислого алюминия может быть комплексной. Т. е. 7-8 кг. сернокислого алюминия на 1м3 арболита и 4 кг. извести на м3 арболита. В случае использования и сернокислого алюминия и извести, приготовление хим. растворов этих минерализаторов надо осуществлять в отдельных емкостях.
2) В смеситель засыпается щепа. Практика показывает, что принудительным смесителям типа РН-300 и им подобным очень тяжело перемешивать заявленный производителем объем. Реально в РН-300 можно засыпать не больше 150 литров щепы. Объем щепы зависит от ее размера.
PS. Требования к щепе: помимо размеров, щепа должна быть с минимальным количеством грязи; количество коры не должны быть более 10-15%; щепа должна быть не свежей, как минимум щепе (дереву) 1-2 месяца должно быть после рубки. Идеальный вариант 3-4 месяца.
3) Запускается смеситель и в процессе перемешивания щепы заливается водный раствор хим. добавок. Если есть возможность распыления этого водного раствора – хорошо. Если нет, то задача при заливке водного раствора состоит в том, чтобы вылить раствор максимально равномерно по всему объему щепы. Т. е. чтобы при заливке раствора намокло как можно больше щепы. Если воду вылить с одной стороны смесителя, то есть вероятность того, что в процессе перемешивания не вся щепа увлажнится. Перемешивание длится минимум 10-20 секунд и после этого засыпается цемент.
4) Цемент засыпается таким образом, чтобы покрыть цементным тестом максимальное количество площади щепок. В идеале 100%. После засыпки цемента перемешивание длится минимум 2-3 минуты.
ВАЖНО:
после того, как в смеситель засыпан цемент, воду в смеситель уже добавлять нежелательно, так как вода смоет со щепок цементное тесто и это может привести к снижению прочности блоков.
5) Смесь после изготовления живет реально 10-15 минут, т. е. за это время смесь надо уложить в форму и спрессовать. С точки зрения удобства изготовления блоков на вибропрессовальном станке, целесообразно устраивать узел перемеса смеси (растворосмеситель) и узел изготовления блока (вибростанок) недалеко друг от друга. Т. е., если смесь из растворосмесителя вывалить на площадку, покрытую листом жести (для лучшего скольжения при накладке смеси в форму), то удобно иметь место самого вибростанка рядом с этой площадкой, чтобы сократить любые расстояния по доставке смеси от смесителя к станку.
6) После того, как форма заполнена арболитовой смесью, включается вибростанок. Процесс вибрирования должен длиться максимум 10-15 секунд. (в зависимости от консистенции смеси и необходимой прочности.) Время вибрирования устанавливается опытным путем. После вибрирования происходит прессование смеси.
ВАЖНО:
7) После изготовления блока поддон с блоком переносится на стеллаж.
8). Складывать блоки один на другой желательно не раньше чем через 3-4 дня. Складывать блоки в 3 ряда в высоту и больше желательно не раньше чем через 6-7 дней после изготовления.
9) Транспортировать блоки можно через 15-20 дней после изготовления при сухой погоде и не ранее чем через 20 дней при сырой погоде.
ВАЖНО:
на разных производствах сроки отгрузки могут отличаться и они зависят от большого количества факторов, начиная с марки и качества цемента и до влажностного режима в помещении и условиях уличного хранения.
- Регистрация:
06.03.08
Сообщения:
27.204
Благодарности:
29.814
4) Производство арболита на станке вибрирование с пригрузом.
Это вариант является одним из наиболее оптимальных способов производства арболита с точки зрения затрат при открытии предприятия. Несмотря на то, что такие станки не продаются в данное время, их устройство не является сложным и позволяет любому промышленному предприятию, изготавливающему станки, изготовить их по тех. заданию заказчика. Более того, простой вариант такого станка можно сделать самостоятельно, с помощью профессионального сварщика. Но надо быть готовым к тому, что придется потратить время на доводку и эксперименты.
На станке вибрирование с пригрузом можно производить как небольшой объем арболита в месяц (150-200 м3), так и значительно больший, от 400 м3 в месяц и больше. В данном разделе будет рассмотрен вариант возможной схемы производства арболита на станке вибрирование с пригрузом объемом не более 200 м3 в месяц за 22 рабочих дня, или до 9 м3 в рабочую 9 часовую смену.
ВАЖНО:
вес пригруза и соответственно коэффициент уплотнения влияет на плотность арболита и соответственно на его прочность. Но зависимость между массой пригруза и коэффициентом уплотнения в какой то момент делает экономически нецелесообразным увеличение массы пригруза.
На рис. 24 приведены кривые зависимости степени уплотнения арболита от удельной величины пригруза; коэффициент уплотнения Куп = H/h,
где Н — высота заполнения формы, мм; h — проектная высота изделия, мм. http://www.stroytechnolog.ru/books/arbolit43.html
Рис. 24. (по ссылке) Влияние удельной величины пригруза на степень уплотнения арболитовой смеси (коэффициент уплотнения Ку)
1 – пригруз 0,02 МПа; 2 – пригруз 0,01 МПа; 3 – пригруз 0,005 МПа; 4 – пригруз 0,003 МПа.
Т. е. видно, что диапазон давления от пригруза может находится в пределах 0,01 МПа и до 0,003 МПа. Значение уплотнения арболитовой смеси (коэффициент 1,27) при вибрировании, равное 0,01 МПа, соответствует уплотнению при прессовании с удельным давлением 0,1 МПа, а воздействие виброуплотнения при пригрузе 0,02 МПа (коэффициент 1,35) соответствует прессованию с усилием 0,35 МПа. Это достигается за счет эффекта псевдоразжижения арболитовой смеси при уплотнении вибрированием с пригрузом. Дальнейшее повышение величины пригруза (более 0,02 МПа) и времени воздействия вибрирования под пригрузом в меньшей степени способствует уплотнению арболитовой смеси. Так, при изменении пригруза с 0,01 до 0,02 МПа, т. е. вдвое, коэффициент уплотнения возрастает лишь с 1,27 до 1,34. Структура арболита, полученная при вибрировании с пригрузом при одинаковой средней плотности и прочности, менее подвержена влажностным деформациям (см. табл. 12), чем структура, полученная только прессованием, что объясняется, очевидно, наличием напряжений в изделии, характер и величина которых зависят от способа формования.
Таблица 12. Влияние способа уплотнения арболитовой смеси на относительные деформации и давление набухания арболита (табл.12 по ссылке)
http://www.stroytechnolog.ru/books/arbolit42.htm
1 МПа = 10,197 кг/см2.
0,1 МПа = 1,02 кг/см2.
0,02 МПа = 0,20 кг/см2.
0,01 МПа = 0,10 кг/см2.
0,005 МПа = 0,05 кг/см2.
0,003 МПа = 0,03 кг/см2.
Исходя из этих данных подбирается вес пригруза. Например при давлении пригруза в 0,01 МПа = 0,10 кг/см2. на смесь получается, что для производства 1 блока арболита размером 50х30х20 (h), площадь поверхности которого равна 1500 см2 вес пригруза нужен 150 кг. (1500 х 0,1 = 150 кг.) А при давлении пригруза в 0,003 МПа = 0,03 кг/см2. на смесь получается, что для производства 1 блока арболита размером 50х30х20 (h), площадь поверхности которого равна 1500 см2 вес пригруза нужен 45 кг. (1500 х 0,03 = 45 кг.)
На сегодняшний момент для производства арболита на станке вибрирование с пригрузом надо исходить именно из этих цифр, т. к. по ним Наназашвили были проведены полноценные исследования.
Для производства такого объема арболита с использованием станка вибрирование с пригрузом и стеллажей необходимо:
1) помещение с площадью минимум
400 м2. В таком помещении должна быть возможность разместить помимо оборудования и емкостей небольшой склад с цементом; стеллажи для складирования арболита, произведенного не менее чем 3 рабочими сменами, т. е. 27 м3.
2) иметь 2 смесителя принудительного типа, например РН-300.
3) емкости, в которых будут разбавляться хим. добавки.
4) мерные емкости, которыми будут в смеситель засыпаться цемент и щепа.
5) 2 тележки, на которых от смесителя арболитовая смесь будет подвозиться к станку.
6) станок вибрирование с пригрузом. Форма будет входить в комплект станка.
7) небольшие поддоны из фанеры или стали на 1 блок, на которых будет происходить формование блока. Таких поддонов надо не менее чем на 27 м3. арболитовых блоков.
8) стеллажи для складирования поддонов с изготовленным арболитом.
9) деревянные поддоны, на которые будет складываться готовый арболит.
10) гидравлический штабеллер.
Процесс производства арболитового блока на станке вибрирование с пригрузом:
1) В емкости с водой заранее разбавляются хим. добавки, например хлористый кальций или сернокислый алюминий из расчета 10-12 кг/м3 арболита (для лиственницы в 2 раза больше). Перед использованием надо раствор перемешать.
ВАЖНО:
хим. добавка на основе сернокислого алюминия может быть комплексной. Т. е. 7-8 кг. сернокислого алюминия на 1м3 арболита и 4 кг. извести на м3 арболита. В случае использования и сернокислого алюминия и извести, приготовление хим. растворов этих минерализаторов надо осуществлять в отдельных емкостях.
2) В оба смесителя засыпается щепа. Практика показывает, что принудительным смесителям типа РН-300 и им подобным очень тяжело перемешивать заявленный производителем объем. Реально в РН-300 можно засыпать не больше 150 литров щепы. Объем щепы зависит от ее размера.
P. S. Требования к щепе: помимо размеров, щепа должна быть с минимальным количеством грязи; количество коры не должны быть более 10-15%; щепа должна быть не свежей, как минимум щепе (дереву) 1-2 месяца должно быть после рубки. Идеальный вариант 3-4 месяца.
3) При использовании двух смесителей наилучшим вариантом является их одновременный запуск, что практически позволяет иметь готовую смесь с обоих смесителей одновременно. Запускаются смесители и в процессе перемешивания щепы заливается водный раствор хим. добавок. Если есть возможность распыления этого водного раствора – хорошо. Если нет, то задача при заливке водного раствора состоит в том, чтобы вылить раствор максимально равномерно по всему объему щепы. Т. е. чтобы при заливке раствора намокло как можно больше щепы. Если воду вылить с одной стороны смесителя, то есть вероятность того, что в процессе перемешивания не вся щепа увлажнится. Перемешивание длится минимум 10-20 секунд и после этого засыпается цемент.
4) Цемент засыпается таким образом, чтобы покрыть цементным тестом максимальное количество площади щепок. В идеале 100%. После засыпки цемента перемешивание длится минимум 2-3 минуты.
ВАЖНО:
после того, как в смеситель засыпан цемент, воду в смеситель уже добавлять нежелательно, так как вода смоет со щепок цементное тесто и это может привести к снижению прочности блоков.
5) Смесь после изготовления живет реально 10-15 минут, т. е. за это время смесь надо уложить в форму и спрессовать. С точки зрения удобства изготовления блоков на станке, целесообразно устраивать узел перемеса смеси (растворосмеситель) и узел изготовления блока (станок) недалеко друг от друга. Т. е., если смесь из растворосмесителя вывалить на площадку, покрытую листом жести (для лучшего скольжения при накладке смеси в форму), то удобно иметь место самого станка рядом с этой площадкой, чтобы сократить любые расстояния по доставке смеси от смесителя к станку. Но при использовании двух смесителей такое вряд ли получится, поэтому придется использовать тележку по доставке готовой смеси к станку. Этот момент надо смотреть по факту площади помещения и схемы организации производственного процесса.
6) Принцип работы действующего станка вибрирование с пригрузом выглядит так: станок организован таким образом, что блоки формуются в один ряд. Т. е. 5-10 блоков в один ряд. В зависимости от количества одновременно изготавливаемых блоков, подбирается длина станка. Плюсом такой схемы является более узкий по ширине пригруз, который намного легче и сделать и поднимать. На виброплощадку станка кладутся поддоны под блоки рядом друг с другом. Затем на эти поддоны опускается одна общая форма на необходимое количество блоков. Форма фиксируется к станку на период изготовления блоков.
7) Форма заполняется готовой арболитовой смесью.
ВАЖНО:
для правильного распределения смеси надо соблюдать несколько моментов:
а) количество блоков на станке должно быть четным, потому что смесителей 2 шт.
б) количество компонентов, которые загружаются в каждый смеситель должно быть одинаковым.
в) количество компонентов, которые загружаются в каждый смеситель, должно подбираться опытным путем из расчета полной загрузки своей части формы. Т. е. вся смесь с каждого смесителя должна быть уложена в свою часть (половину) формы за один раз.
8) После того, как форма заполнена арболитовой смесью, включается процесс вибрирования. Время процесса вибрирования устанавливается опытным путем в зависимости от консистенции смеси и необходимой прочности. Через некоторое время (либо сразу) включают двигатель, который опускает пригруз. В зависимости от конструкции пригруза, пригруз может опускаться в форму или во время процесса вибрирования или процесс вибрирования надо будет остановить, чтобы пригруз опустился в форму. После того, как пригруз будет в форме, опять включается (или продолжается) вибрирование, в процессе которого смесь оседает не только под воздействием вибрации, но и под воздействием веса пригруза.
ВАЖНО:
вибрирование арболитовой смеси длительное время негативно сказывается на качестве смеси, т. к. при длительном вибрировании значительная часть цементного теста слезает с щепок и стекает вниз.
ВАЖНО:
время вибрирования также зависит от мощности вибраторов.
9) После изготовления блоков форма поднимается, а поддон с блоком переносится на стеллаж.
10). Складывать блоки один на другой желательно не раньше чем через 3-4 дня. Складывать блоки в 3 ряда в высоту и больше желательно не раньше чем через 6-7 дней после изготовления.
11) Транспортировать блоки заказчикам можно через 10-15 дней после изготовления при сухой погоде и не ранее чем через 15-20 дней при сырой погоде.
ВАЖНО:
на разных производствах сроки отгрузки могут отличаться и они зависят от большого количества факторов, начиная с марки и качества цемента и до влажностного режима в помещении и условиях уличного хранения.
Плюсом
этого варианта является механизация процесса изготовления блока, что ускоряет скорость изготовления блоков; более высокая однородность блоков, что увеличивает получение блоков одной и то же плотности; более хорошая геометрия блоков; возможность иметь не очень большое по площади помещение, т. к. на стеллажах блоки можно ставить в 5-7 рядов.
Минусом
этого варианта является необходимость затрат на станок и его амортизацию; наличие большого количества поддонов под каждый блок, т. к. их надо не менее 3х дневных смен. Также к минусам можно отнести необходимость наличия стеллажей.
- Регистрация:
06.03.08
Сообщения:
27.204
http://www.сайт/threads/63106/page-3#post-1613823
Ig Um
, Подмосковье,
geogen
, Ленинградская обл.,
серргей1234
, Сергиев Посад,
ket4up
, Подмосковье,
P. S. Нашел конечно не всех, но по быстрому больше не получилось.
Что такое арболит? Слово арболит имеет происхождение от латинского arbor, «дерево» и litos, «камень». На нашей территории (т.е. бывшего Союза) его называют арболит, а за границей — деревобетон. Деревобетон включает в себя опилки, а арболит только щепу.
Арболит – это материал, состоящий из смеси, в составе которой в качестве вяжущей основы используют цемент (вместо цемента может быть известь, магнезиальное вяжущее), органический заполнитель (древесная щепа), и небольшое количество химических добавок.
История арболита и деревобетона
Отечественный опыт производства арболита
Деревобетон по официальной версии первыми открыли голландцы в 1930-ых годах. Они разработали технологию производства материала под названием DURISOL (ДЮРИСОЛ). Появились представительства компании DURISOL в Швейцарии и Германии. Деревобетон по технологии ДЮРИСОЛ благодаря своим характеристикам и свойствам стал известен во всей Европе и в Северной Америке.
Отечественный опыт производства арболита начинается в 1960-ом году, когда Советский Союз, скопировав технологию ДЮРИСОЛ, разрабатывает по материалу ГОСТ. Русский арболит проходит все технические испытания, даже становится стандартизированным и сертифицированным в СССР. На территории Союза строят более сотни заводов по производству арболита и материал начинают применять для строительства заводских зданий, сельских домов и ферм.
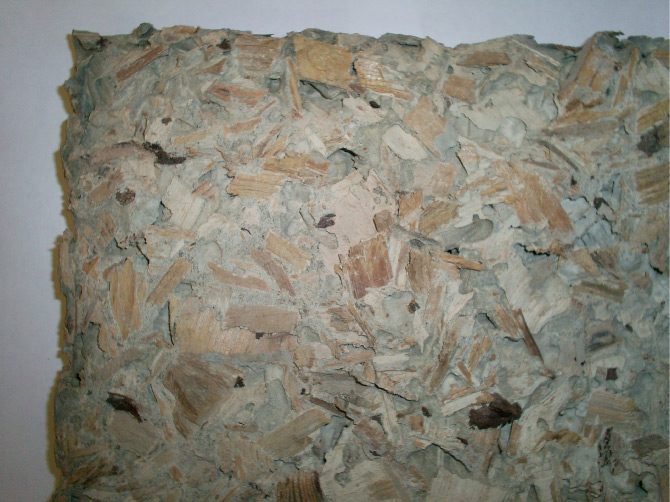
Арболит из щепы
Интересный факт, что в 60-ые годы панели арболита применялись при строительстве трех здания и столовой в Антарктиде, на станции «Молодежная». Несмотря на климат, толщина стен была всего 30 см, и этого было достаточно.
Советский союз в 80-ых годах разрабатывает целевую программу под названием «Арболит». По этой программе заводы, производящие стройматериал, начинают работать с мощностью выпуска изделий в 500 тыс. м3 в год, а из советского арболита строят более 3 тыс. зданий.
В 1990-ые годы взят ориентир на строительство домов из блоков и панелей на основе неорганического заполнителя. Арболит, несмотря на свои уникальные свойства, массового применения в советском масштабном домостроении не получил. Одни арболитовые заводы были развалены, другие перепрофилированы, и в целом эта индустрия была разрушена. А те здания, что еще в 60-ые были построены из арболита, сейчас стоят, не утратив своего первоначального вида и состояния.
Зарубежный опыт производства деревобетона
В настоящее время компания DURISOL имеет свои представительства в 12 странах мира, в т.ч. в Республике Беларусь и Российской Федерации. Деревобетон ДЮРИСОЛ состоит из щепы хвойных деревьев (80-90% от всего объема), которую обрабатывают минеральными добавками и портландцемента.
Фирма «Duripanel» в Германии выпускает блоки из деревобетона, наряду с блоками выпускает также стеновые панели. Панель имеет трёхслойную структуру, жёсткую основу внутри и с обеих сторон гладкий верхний слой. Для изготовления панелей используют древесные волокна, минеральные добавки, воду и портландцемент в качестве вяжущего.
Уже на протяжении 50-ти лет австрийская фирма занимается производством несъемной опалубки. Опалубка состоит из спрессованной еловой древесной щепы (95% от всего объема), цемента, жидкого стекла и сульфата алюминия.
В Японии выпускают древесно-цементные плиты «Пермакс». В качестве заполнителя используются заготовки древесины мягких пород и отходы от производства фанеры, из которых на строгальных станках изготавливают продольную стружку. Стружка высушивается, после чего древесное волокно расстилают ровным слоем на специальной распределительной машине и пропитывают цементным раствором с добавкой минерализаторов. Кроме древесного волокна для плит «Пермакс» применяют древесную щепу. В Японии выпускают около 20 млн. штук таких плит в год, их производство развивается также в соседних странах (Таиланд, Филиппины и др.)
- Сenturyboard (Япония и США).
Фирма «Сenturyboard», специализирующаяся в области лесопильной промышленности, организовала производство огнестойких плит для наружной отделки. Плиты покрываются акриловой краской или синтетическими смолами и имеют хороший внешний вид.
Фирма «Faswall» изготавливает блоки, которые состоят из портландцемента, древесной щепы и золы-уноса. Блоки соответствуют всем американским стандартам и широко применяются уже в течение 60-ти лет.
- Lignacite ltd (Великобритания)
Компания «Lignacite ltd» разработала строительные блоки на основе хвойных опилок, песка и цемента. Блоки пустотелые, обладают хорошими свойствами теплоизоляции, водостойкие, огнестойкие, морозостойкие и биостойкие. Применяют их для наружных и внутренних стен при малоэтажном строительстве.
В Словакии разработан эффективный стеновой материал. Пилинобетон состоит из древесных отходов – опилок и стружки из хвойных пород древесины, хлористого кальция и портландцемента. Применяется для строительства сельскохозяйственных и жилых зданий, строительство мансард. Экологичность и долговечность деревобетона позволяет найти для него неожиданное применение. В Великобритании было организовано производство скворечников из деревобетона.
Состав арболита
Для изготовления арболита применяют состав со следующими компонентами: органический заполнитель, цементное вяжущее, вода и химические добавки.
Заполнитель
Арболитовой основой является заполнитель: его количество в объеме материала составляет 75-95%. В качестве заполнителя в основном выступает (по-другому — измельченная дробилкой древесина). Для обеспечения лучших технических характеристик материала оптимальным вариантом выбора является щепа деревьев хвойных пород, кроме лиственницы. Также можно использовать щепу березовую, осиновую, тополиную, т.е. деревьев твердолиственных пород.
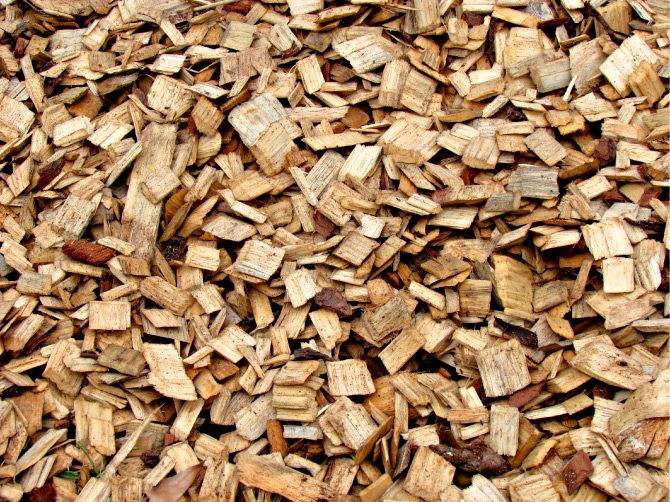
Щепа для арболита
Древесная щепа должна быть определенного размера. Ее изготовление из свежесрубленных деревьев запрещено т.к. там большое количество не разложившихся или не окислившихся сахаров, которые пагубно влияют на характеристики. Некоторые, для придания гладкой поверхности щепу смешивают с опилками со стружкой.
Вместо древесной щепы известно также применение другой органики, но это уже разновидности деревобетона: обработанная костра льна (костробетон) или костра конопли, измельченная рисовая солома или измельченные листья хлопчатника.
Цементное вяжущее
В качестве цементного вяжущего обычно используют портландцемент, марки 400 и 500. Расход цементного вяжущего зависит от требуемых характеристик изготовляемого арболита, от его марки, от вида выбранного заполнителя, от марки портландцемента и т.д.
Вода
Основная сложность при производстве изделий из арболита – необходимость добиться увеличения прочности цемента за счет погашения вредного влияния органического заполнителя. Органика выделяет сахара, которые негативно сказываются на прочности цементного вяжущего. Вода растворяет многие из них. Щепу выдерживают в воде от трех месяцев на открытом воздухе. Вместо воды часто используют известковый раствор, в котором 3-4 дня вымачивают щепу.
Химические добавки
Для нейтрализации вредных веществ древесного заполнителя наряду с замачиванием в воде или известковом растворе применяют различные химические добавки. Этот процесс называется минерализация.
Щепу обрабатывают растворами сульфата алюминия, хлористого кальция, гашеной извести, сернокислого глинозёма и другими минерализаторами.
Вышеперечисленные добавки могут использоваться в двух вариантах: первый вариант — минерализация, т.е. обработка только щепы; второй вариант — ускоритель твердения цементного камня, т.е. на стадии замеса цемента, щепы и воды.
Количество химической добавки для арболита обычно составляет 2-5% от веса цемента. Их можно использовать по отдельности или смешивать друг с другом. Марка арболита напрямую зависит от количества используемого химического компонента.
Применение арболита в строительстве
Существует три вида арболита: конструкционный, теплоизоляционный, конструкционно-теплоизоляционный (комбинированный).
Содержит в составе большее количество цементного вяжущего и имеет более высокую плотность (500-800 кг/м3). Из конструкционного вида строят несущие стены.
В составе смеси присутствует больше щепы чем в конструкционном, плотность более низкая (до 500 кг/м3). Теплоизоляционный арболит применяют при строительстве перегородок.
- Комбинированный (конструкционно-теплоизоляционный)
Имеет среднюю плотность от 450 до 600 кг/м3. Совмещает в себе свойства как конструкционного, так и теплоизоляционного вида арболита.
В строительстве используют арболитовые блоки, плиты, панели, а также монолитный (жидкий) арболит.
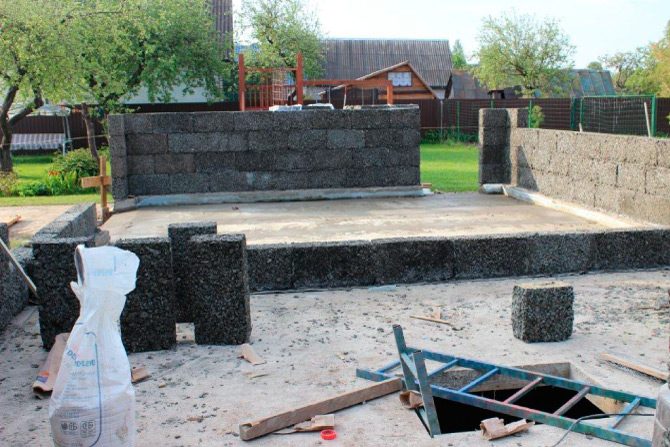
Арболитовые блоки
Что строят из арболита? Из арболитовых блоков и монолитного арболита строят дома и коттеджи (до 3-х этажей), бани, гаражи и другие хозяйственные постройки. Этот стройматериал может выступать в роли теплоизолятора и звукоизолятора при утеплении стен, полов и потолков зданий.
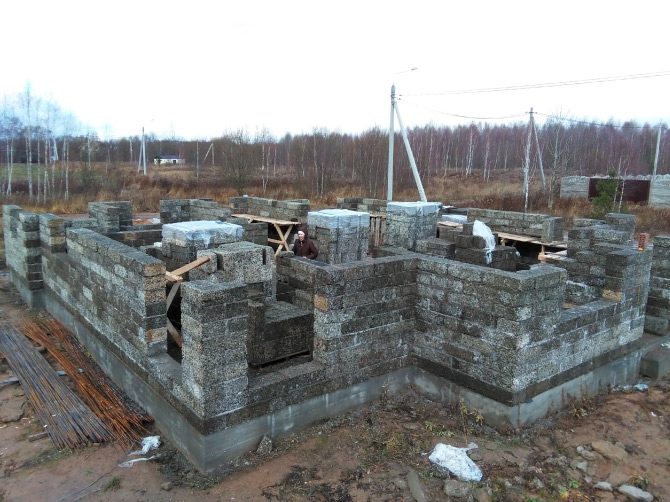
Строительство дома из арболитовых блоков
Плюсы и минусы арболита
Арболит состоит в основном из древесины, поэтому его свойства при использовании в строительстве обладают рядом преимуществ, в сравнении с другими материалами.
Достоинства арболита
- как теплоизоляционный материал имеет хорошую теплопроводность
- материал имеет высокий показатель паропроницаемости, немного уступающий дереву
- высокие показатели теплоемкости. Его аккумулирующие свойства, позволяют долго сохранять тепло в доме, т.е. отсутствуют резкие скачки температуры. Значение теплоемкости арболита более чем в 3 раза превышает значение теплоемкости газосиликата, пенобетона, минваты, полистиролы и др.
- не горит, не тлеет и при контакте с огнем практически не образует дыма
- при различных деформациях или усадки фундамента здания строительный материал с легкостью принимает нагрузки на растяжение, не трескаясь
- высокие показатели морозостойкости материала, при отсутствии постоянной сырости
- изделия из арболита имеют небольшой вес
- удобство использования в строительстве, так как материал хорошо режется, в него можно вкручивать саморезы, вбивать гвозди, он отлично держит крепеж
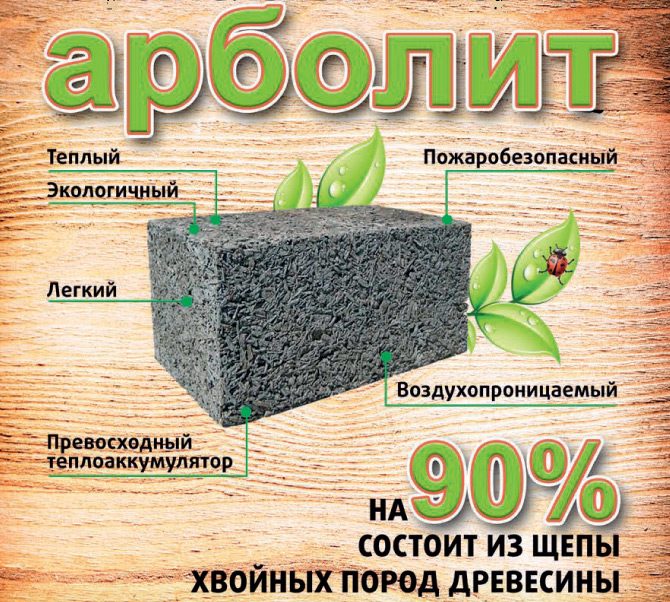
Достоинства арболита
Недостатки арболита
Свойства, которые можно отнести к недостаткам напрямую зависят от технологии производства материала, подбора состава, соблюдения инструкций изготовления арболита и условий хранения. Например, характеристики материала зависят от применения того или иного химического компонента, пропорции смеси арболита, размера щепы, условий утрамбовки, условий отвердевания и других факторов.
Поэтому недостатки арболита это понятие относительное:
- боится постоянной высокой влажности и отсутствия вентиляции
В условиях постоянной влажности и отсутствия вентиляции на стене из любого материала будет образовываться плесень.
К главному недостатку можно отнести невысокую прочность, и согласно нормативным документам арболит можно использовать только при малоэтажном строительстве или в качестве теплоизолирующего материала.
Но весь вопрос: с чем мы сравниваем прочность? Если с тяжелым бетоном, то естественно прочность арболита ниже. А если сравнить с тем же пенобетоном или газосиликатом, то значения прочности практически одинаковые.
Тем более были проведены исследования и разработаны рецептура и современные технологии изготовления материала, позволяющие повысить показатели прочности арболита.
Если из этой обзорной статьи вы так и не узнали что такое арболит, то можете оставить комментарии ниже и задать нам более детальные вопросы. Мы обязательно на них ответим.
1. Заполнители растительного происхождения.
Основой арболита могут быть заполнители на основе целлюлозы:
- измельченная древесина;
- костры конопли;
- костры льна;
- измельченные стебли хлопчатника;
- измельченная рисовая солома и др.
Важными характеристиками строительного материала являются его прочность (какую нагрузку выдерживает) и теплопроводность (насколько материал теплый). Например, кирпич прочный, но холодный материал. Утеплители, наоборот, обладают малой прочностью, но является низкотеплопроводными (теплыми).
Характеристики арболита в зависимости от вида органического заполнителя также могут существенно различаться. При правильной технологии производства арболит на основе древесины имеет лучшее соотношение прочности и теплопроводности.
Например, для строительства двух или трехэтажных зданий с использованием железобетонных перекрытий необходима прочность B2,5 или выше. Такой прочности можно добиться при производстве арболита на основе измельченной древесины.
В этой статье будем рассматривать арболит только на основе измельченной древесины.
Обратим внимание, что измельченная древесина — это не опил и не стружка. Измельченная древесина — это щепа, размеры которой установлены ГОСТом. Размеры частиц не должны превышать 40мм X 10мм X 5мм. Для получения щепы нужного размера ее пропускают через щепорубильные машины, а затем сита с ячейками нужной величины.
Используется щепа, полученная из остатков деловой древесины, с примесью коры не более 5%. Только сосна. Щепа для арболита производится в 4 этапа:
1. Измельчение древесины барабанной дробилкой.
2. Дробление молотковой дробилкой.
3. Просеивание через сита.
4. Удаление пылевидной фракции.
Измельченная древесина связывается цементом. По ГОСТу используется цемент не ниже 400 марки прочности или портландцемент класса не ниже 42,5.
Чем выше марка прочности цемента, тем легче произвести прочный арболит.
Используется цемент Сенгилеевского цементного завода. Марка прочности — 500. Предназначен для изготовления высокопрочных бетонов.
3. Добавки для приготовления арболита
В обычных условиях древесная щепа не соединяется с цементом. В древесине содержатся сахара, которые являются ядом для цемента. Поэтому получить прочный строительный материал невозможно.
В процессе производства арболита щепа проходит обработку — минерализацию. От этого этапа зависит:
- прочность арболита;
- подверженность гниению;
- долговечность постройки.
ГОСТ при производстве арболита предлагает использовать:
- Хлорид кальция (пищевая добавка E509);
- Сернокислый глинозем или сульфат алюминия (пищевая добавка E520);
- Жидкое стекло;
- И т. д.
Перечисленные добавки используются также в пищевой промышленности, медицине, сельском хозяйстве и т. д.
Разные производители арболита используют разные добавки. Обычно, это 1-2 вещества из перечисленного списка. Главная их задача — нейтрализация вредного влияния древесных сахаров. Содержание сахара по ГОСТу не должно быть больше 2%.
Некоторые добавки не удаляют сахара из щепы, а временно блокируют их влияние. Таким образом действует, например, жидкое стекло. Оно обеспечивает хорошее сцепление древесной щепы с цементом в процессе производства, но может снизить срок службы постройки в долгосрочной перспективе.
Используются 2 добавки: гашеная известь (Е526) и хлорид кальция (Е509).
Гашеная известь используется на этапе минерализации древесной щепы. Позволяет снизить уровень содержания сахаров до 1%.
Хлорид кальция является ускорителем твердения цемента и повышает адгезию (сцепление) цемента и щепы.
Будем рассматривать арболит с плотностью D650 и маркой прочности до В2,5.
Теплопроводность арболита — до 0,12 Вт/(м*C)
Чем ниже теплопроводность стенового материала, тем теплее дом. У арболита самая низкая теплопроводность среди конструкционных материалов. Для примера средняя теплопроводность:
- газобетона — 0,18. В 1,5 раза холоднее арболита.
- керамического пустотелого кирпича — 0,41. В 3,5 раза холоднее арболита.
- керамзитобетона — 0,66. В 5,5 раз холоднее арболита.
- дерева — 0,14. В 1,3 раза холоднее арболита.
Для постройки теплого дома из арболита в Центрально-Европейской части России достаточно стены толщиной 30 см. Для постройки энергоэффективного дома — 40 см.
Арболит Larbi.
Имеет теплопроводность — 0,11 Вт/(м*С).
Биостойкость
Сделанный по ГОСТу и прошедший минерализацию арболит — биостойкий материал. Это означает, что он не подвержен гниению, воздействию разрушающих дерево микроорганизмов и насекомых. Его не испортят грызуны.
Арболит Larbi.
Проходит глубокую минерализацию, остаточное содержание сахаров в древесине Larbi — не более 1%.
Ваш браузер не поддерживает тег video
Морозостройкость
Морозостойкость — это количество циклов замораживания и оттаивания, которое выдерживает материал. Конструкционный арболит выдерживает до 50 таких циклов. Аналогичен показателю морозостойкости керамического кирпича и больше показателя морозостойкости газобетона в 1,4 раза.
Арболит Larbi.
Имеет показатель морозостройкости — F50.
Паропроницаемость — 0,18 мг/(м*ч*Па)
Упрощенно, паропроницаемость — это способность стенового материала пропускать влагу.
Это важный параметр при проектировании стены дома. Использование материалов с разной паропроницаемостью может привести к накоплению влаги внутри стены, выпадению конденсата и образованию плесени.
- 1.
Арболит обладает высокой паропроницаемостью — 0,18 мг/(м*ч*Па). Примерно такая же паропроницаемость у керамического пустотелого кирпича, газобетона или керамзитобетона.
- 2.
Для создания комфортного воздухо- и теплообмена в помещении паропроницаемость стены из арболита необходимо уменьшить, но не ограничить полностью.
- 3.
Применение утеплителей с низкой паропроницаемостью может привести к:
- накоплению влаги внутри стены;
- снижению воздухообмена помещения с внешней средой;
- снижению экологичности конструкции.
- 4.
Для создания нужного уровня паропроницаемости стену из арболита необходимо оштукатурить в сответствии с ГОСТом:
- Толщина внутреннего штукатурного слоя — 15 мм;
- Толщина внешнего штукатурного слоя — 20 мм.
- 5.
При этом влага не будет накапливаться или задерживаться в стене.
- 6.
Для оштукатуривания стены используется смесь, которая является:
- паропроницаемой;
- пластичной;
- эластичной.
Это могут быть цементно-песчаные штукатурки с добавлением гашеной извести или гипса. Например.
Этот материал для строительства объектов различного предназначения применяют более пятидесяти лет. При всей своей популярности арболит имеет положительные и отрицательные свойства. В советское время для строительства жилых домов этот материал использовали редко, отдавая предпочтение натуральной древесине, кирпичной кладке или сборным бетонным конструкциям. Сегодня арболит обрел популярность при сооружении всевозможных объектов.
Краткое описание арболита
Итак, что такое арболит?
Своим названием материал обязан французам. В переводе с их языка это означает «дерево».
Арболит от простого материала отличается методом изготовления. Его укладывают в форму для арболита или опалубочную конструкцию в жидком состоянии. Высыхая, материал получает проектные качества прочности.
Сам арболит и изделия из него должны соответствовать общим техническим условиям, определенным ГОСТом 19222 84 и ГОСТом 54854 2011.
Состав
Второе название – древобетон, для производства которого используют три основных ингредиента:
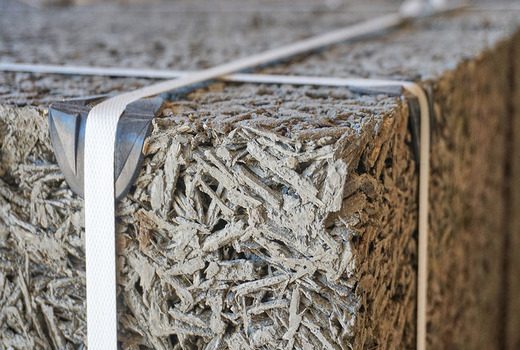
Больше всего в составе используют древесную стружку, которую иногда заменяют опилками. Качество таких блоков несколько хуже, да и эксплуатационные данные оставляют желать лучшего. Блок получается более плотным и тяжелым, подвержен деформированию. Но есть некоторые достоинства – такая разновидность арболита отличается приемлемой стоимостью.
Ко всем компонентам арболита добавляется вода.
Различают два вида арболита:
- Конструкционный – содержит много цемента, отличается повышенным показателем плотности, достигающей 500 – 800 килограмм на метр кубический. Из этого арболита строят стены.
- Теплоизоляционный – в него добавляют много щепы, от чего плотность не превышает пятисот килограмм на кубометр. Из такого материала возводятся перегородки, в несущей стене его применяют в качестве утеплительного материала.
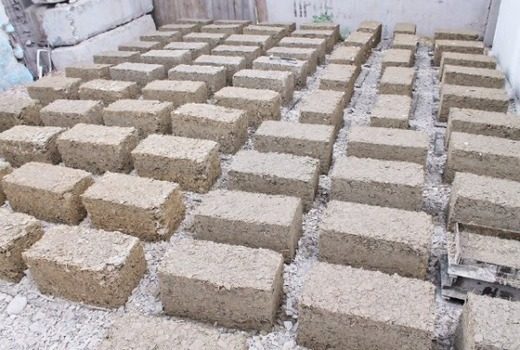
Выпуск материала налажен в двух формах:
- блочная – изделия отличаются определенными размерами. Гостом установлены не только параметры, но и разрешенные отклонения. В итоге размерная погрешность несколько выше, и это следует учесть во время ведения работ, иначе между блоками получатся швы, отличающиеся между собой по толщине. Блок позволяет максимально сократить строительные сроки, потому что рабочий темп задается только временем, необходимым для застывания раствора;
- монолитная – изготавливается непосредственно на строительной площадке и сразу применяется, так как хранить такой материал невозможно. Больше всего монолитный вариант используется при утеплении. Но известны случаи, когда монолитным способом строили небольшие объекты.
Приготовление монолитного материала удешевляет строительный процесс, только скорость работ снижается. В отличие от остальных разновидностей бетона этому материалу необходимо много времени, чтобы стать прочным.
Технология производства
Изготовление включает несколько рабочих этапов. На автоматической линии для арболита предварительно выполняется дробление стружки, потом – ее сортировка. Чтобы наполнитель состоял из частиц нужного размера, стружку пропускают через сито.
После этого наполнительный компонент обеспыливается. Его смешивают с цементом, химическими компонентами и водой. Подготовленный раствор выливается в формы, изготовленные из металла. Это помогает получить ровные блоки с гладкой поверхностью.
Смесь, залитая по формам, утрамбовывается при помощи вибропресса и выдерживается до полного отвердения. До отправки на строительную площадку блоки просушиваются в течение двух недель, пока не станут достаточно прочными.
А как делают арболит в домашних условиях? Такой процесс тоже подразумевает соблюдение некоторых технологических особенностей.
Формы разрешается сделать из толстых досок, чтобы можно было при необходимости их разобрать.
Если соблюдать рецепт арболита по ГОСТу, то на 1 м3 сырья потребуются следующие пропорции ингредиентов:
- портландцемент М500 в количестве 250 – 300 кг;
- столько же стружки;
- 400 л воды;
- химические добавки в количестве 2 – 4 % от всего веса.
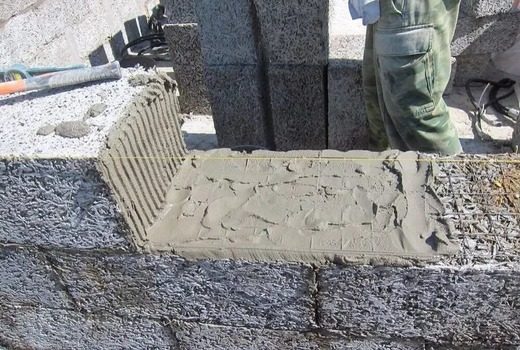
Известны рецептуры, по которым в качестве исходного сырья дополнительно используют:
- жидкое стекло для арболита;
- хлористый кальций для арболита;
- сульфат алюминия для арболита;
- пластификаторы для арболита.
Стружка просеивается, чтобы удалить крупные частицы. Потом ее высыпают в бетоносмеситель, заливают воду, в которой предварительно растворены добавки. Все смешивается, после чего добавляется цемент. Состав, получивший однородность, выкладывается в формы, предварительно смазанные известковым раствором. В момент укладки смесь тщательно трамбуется, чтобы до верхнего края она не доходила сантиметра на два. Оставшийся объем заполняется штукатурной смесью.
Приготовленный по такому рецепту арболит выдерживается в формах минимум сутки, после этого его отправляют под навес на двухнедельную просушку.
Про материал, приготовленный таким способом, есть положительные отзывы. Самодельный арболит отлично подходит для возведения стен и перегородок.
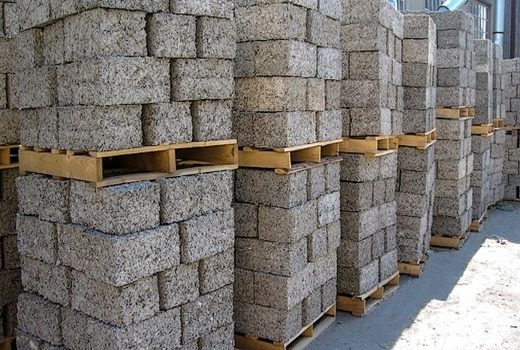
Области использования
Материал используют главным образом в частном строительстве для возведения малоэтажных объектов. Из него изготавливаются блоки и панели различных размеров.
За границей такие блоки иногда применяют при строительстве многоэтажных домов и промышленных объектов. Некоторые изготавливают из арболита фундаментное основание, на котором устанавливают стены для гаража или постройки хозяйственного назначения.
Кроме этого, арболитовую смесь используют в качестве теплоизоляторного материала в каркасных постройках. Кроме того, ей заполняют стены при строительстве колодцевых кладок.
Достоинства и недостатки
Как любой строительный материал, древобетон отличается своими положительными и отрицательными качествами. Из-за низкого показателя прочности его не применяют при строительстве высотных зданий, но в качестве утеплительного материала он вполне подходит.
Рассмотрим положительные характеристики материала:
- теплоизоляционный показатель – самая примечательная особенность арболита. Теплопроводность его составляет 0.08 Вт, что значительно лучше, чем у различных бетонов и кирпича;
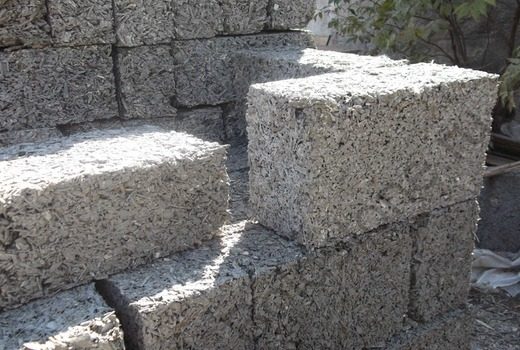
- арболит считается аккумулирующим материалом, способен сохранять тепло в помещении из древобетона. Резких температурных перепадов не наблюдается;
- степень горючести материала низкая, он считается трудновоспламеняемым, образует минимальное количество дыма. Его смело относят к пожаробезопасным;
- паропроницаемость высокая. Естественно, что у древесины данный показатель выше, но многие потребители при строительстве бани предпочитают именно арболит, а не другие виды каменных материалов. К тому же, для такого объекта учитывается и огнестойкость арболита;
- прочность конструкционного арболита равна В3.5, так что из древобетона строятся объекты, высота которых не превышает трех этажей. Но арболит отлично противостоит нагрузочным воздействиям на растяжение. Это означает, что во время подвижек и усадки фундаментной основы материал не покроется трещинами, самостоятельно компенсируя все смещения;
- морозостойкость зависит от класса материала и варьируется в пределах F25 – 50. Но если морозы сочетаются с сырой погодой, то срок службы арболита существенно сокращается;
- материал отлично пилится, разрезается, неплохо удерживает в себе крепежные элементы. Он действительно считается отличным решением для объектов хозяйственного предназначения. Если не знаете, чем пилить арболит, смело берите в руки обычную ножовку;
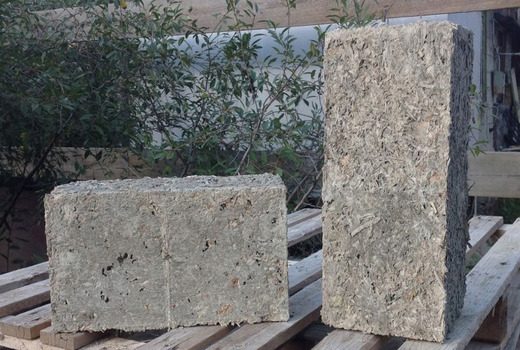
- вес арболитового блока небольшой, что позволяет сократить сроки строительных работ;
- поверхность отлично штукатурится, нет необходимости применять сетку;
- прочность материала высокая – М10 – 25. Даже начинает казаться, что в процессе изготовления применяли пресс;
- изделия из арболита отличаются хорошей звукоизоляцией. Такой эффект возможен благодаря тому, что внутри блока имеется огромное количество пустот, образованных щепой древесины. Кстати, такая структура оказывает влияние на продуваемость материала.
Как видите, достоинств много, но имеются и негативные моменты:
- свойства влагопоглощения – не следует использовать материал в строительстве помещений с заведомо высоким содержанием влаги в воздухе. Древобетон впитывает много воды, но удерживать ее не способен. Если блок погрузить в воду, потом достать, то жидкость стечет, а блок подсохнет. Такая особенность позволяет применение арболита для строительства бани, потому что помещение относится к группе постоянно отапливаемых;
- слабая прочность материала, из-за которой его используют в малоэтажном строительстве и в качестве утеплителя;
- долговечность материала – вопрос открытый. Нет еще достаточного количества данных по эксплуатации, да и многое здесь зависит от качественных показателей арболитного сырья. Одним словом, максимальный срок службы арболита не установлен;
- материал арболит, изготовленный по ГОСТу, может сравниться с пенобетоном. Поэтому стоимость его не самая дешевая. Данный фактор определяется еще и автоматизированной технологией производства.